Compressed Air
Compressed air systems are not only used to run certain tools in the fabrication process, but they also play a critical role in the maintenance and upkeep of metalworking machines. In the machining process, compressed air systems are commonly used to remove dust, dirt, oils, chips, and other debris from a workpiece that have accumulated in the cutting or forming process, along with other contaminants that may become trapped within cutting tools or cutting surfaces. Many compressed air systems used for maintenance purposes incorporate some form of air drying system, so that the compressed air expelled does not contain high levels of moisture that may condense on surfaces and cause corrosion.
The Cost, Common Culprits, Detection and Repair of Compressed Air System Leaks
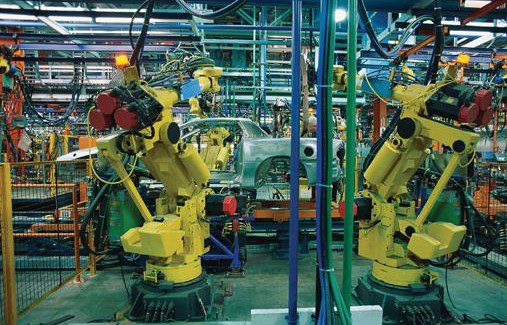
An ongoing leak detection audit and repair program will quickly pay for itself through energy savings (and may even be subsidized by local utility incentive programs). Equally important, you will likely see benefits from reduced downtime and better running production equipment. All of these contribute to a stronger bottom line.
An ongoing leak detection audit and repair program will quickly pay for itself through energy savings (and may even be subsidized by local utility incentive programs). Equally important, you will likely see benefits from reduced downtime and better running production equipment. All of these contribute to a stronger bottom line.
A case study showing the technical capabilities and solutions from EXAIR Corporation.
Even though a machine tool spindle is a high-precision machine component, more often than not it is handled carelessly, forced to perform well beyond design limitations, or otherwise abused to the breaking point. Ed Zitney of SKF Machine Tool Services shows how proper care and maintenance can make all the difference in both its operation and longevity in service.
PneuTech highlights its TNX Series Expandable Membrane Nitrogen Generators. They are designed to offer scalable and efficient nitrogen generation for a variety of industrial applications.
EXAIR’s TurboBlast Safety Air Gun is an ideal solution for blowoff applications requiring maximum force such as removing stubborn or heavy debris like slag and flash and so on.
Designed to address a wide range of cooling challenges, this tool offers precision control, versatility, and ease of use for a variety of applications including milling, machining, soldering, gas sampling, welding and more.