Column
Filter by Process Zone:
Firing Up Growth with Design Collaboration
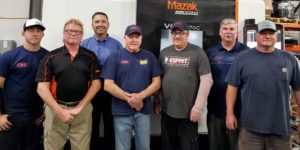
As heavy equipment manufacturers gear up for healthy backlogs, a key West Coast supplier is helping customers find reliable and cost-saving replacements for obsolete parts. Meet the former chef-cum-machinist who’s serving up all kinds of new orders via his CAM software.
Design Is Destiny If You Want To Optimize Beveling
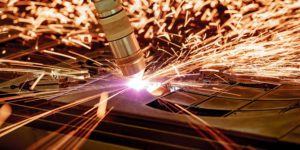
Even the most sophisticated nesting software won’t eliminate the need to manually finish an edge if the job’s not thought through from start to finish. Follow these three best practices to minimize wasted time and material.
How to Protect Your Metalworking Business From Cyber Extortion
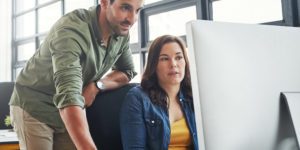
A preventative cybersecurity plan helps mitigate damage by outlining next steps once data is compromised. But what about legal fees and public relations expenses to repair potential damage to your company’s reputation?
Using Intelligent Machine Control To Optimize Quality Assurance
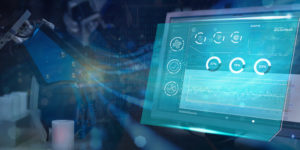
One of manufacturing’s biggest challenges is filling the knowledge gap left by skilled employees who retire. Intelligent machine control (IMC) increases throughput regardless of who’s operating measurement and production equipment by removing the potential for human error.
To Balance, Or Not To Balance? Toolholders, That Is
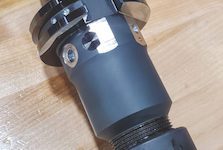
It’s time for machine tool builders and machining companies to shelf the long-standing ISO 1940-1 standard in favor of ISO 16084:2017. Not only is balancing tools rarely necessary, it can also be risky.
A Faster, More-Accurate Way to Tap and Drill Structural Steel
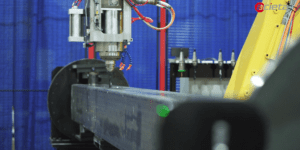
A heavy equipment manufacturer is using a 6-axis robotic arm equipped with a drilling spindle to very precisely make holes in structural steel up to 1 inch thick. The solution is one-third the cost of traditional drilling but performs many other applications and requires just one operator.
Understanding Welding Slag in Flux-Cored Processes
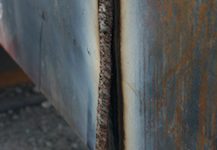
Slag is more than a bothersome byproduct. It plays an important role in ensuring good weld quality, and the various slag systems also impact a wire’s welding characteristics.
How to Get the Most Out of Today’s Sheet Metal Laser Cutters
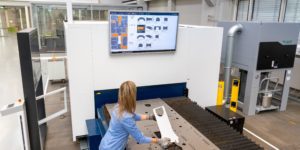
There’s a big difference between just cutting fast and achieving impressive throughput. As machines become faster, factories must properly manage downstream handling processes.
How to Minimize Post-Processing Headaches for 3D-Printed Parts
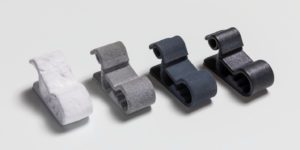
Although 3D metal printing is becoming more popular, finishing remains a challenging and arduous task. Understanding how post-processing works and how to measure results will help you optimize this crucial step.
Improve Band Sawing Operations with These Solutions to Three Common Challenges

Impediments to fully optimized band sawing can be broken into three broad categories: teeth problems, blade problems, and cutting problems. These troubleshooting tips will help operators of all experience levels work as efficiently as possible.
Eight Tips for Getting ERP Right the First Time
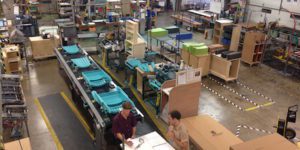
Done right, enterprise resource planning (ERP) identifies and systematically eliminates activities that eat into profits. Here’s how to select a program and partner that will facilitate rather than frustrate the process.
Three Ways to Cut Field Welding Costs
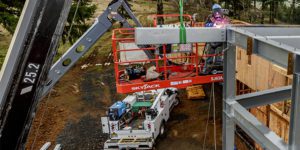
Walking back and forth to a vehicle to tweak an engine-driven welder/generator’s control panel takes time. Remote control devices increase productivity by putting the ability to make changes in the palm of the operator’s hand.