Tom Bailey

Articles by Tom Bailey
Cobotic Welding Gets Serious
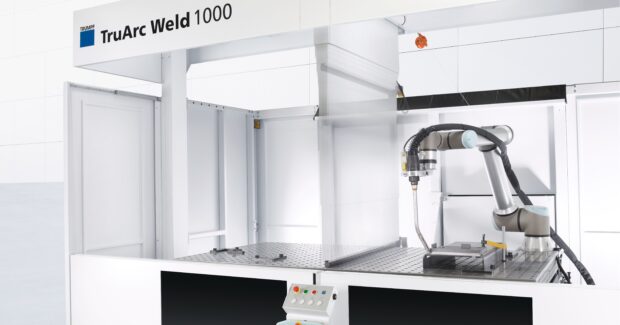
With the addition of intelligent functionality, cobotic arc-welding cells are only becoming more profitable for any shop to operate.
Artificial Intelligence Joins the Fabrication Shop
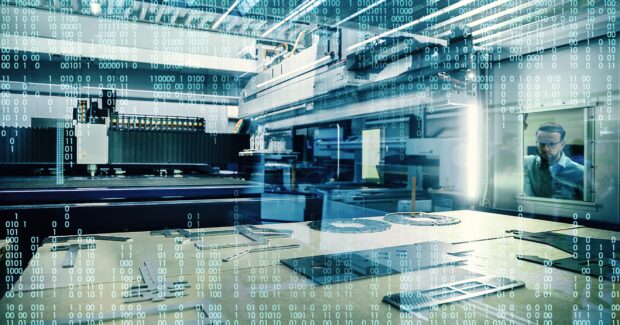
AI-based assistants will not only help factories operate in a smarter way, but they will also have a dramatic impact on manufacturing profitability as well.
Ultra-High-Power Lasers Tackle Ultra Heavy Plate
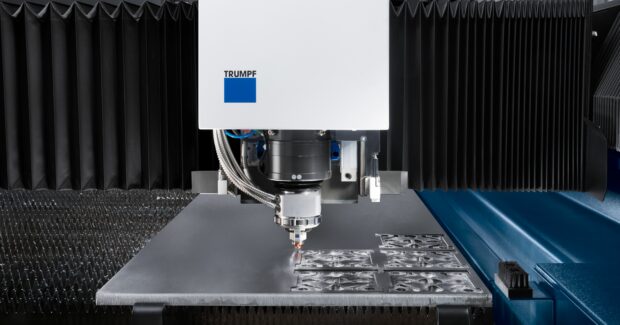
With more than 20 kilowatts of power available, cutting thickness limits can be pushed to as thick as 2”, allowing fabricators to bring the speed, precision and cutting quality of the laser to a new range of parts and products.
The Economics of Scale: Coil-Fed Laser Processing

The advent of turnkey and completely integrated coil-fed laser processing systems promises to enable serious reductions in part costs.
Cobots as Flexible Fab Shop Tools
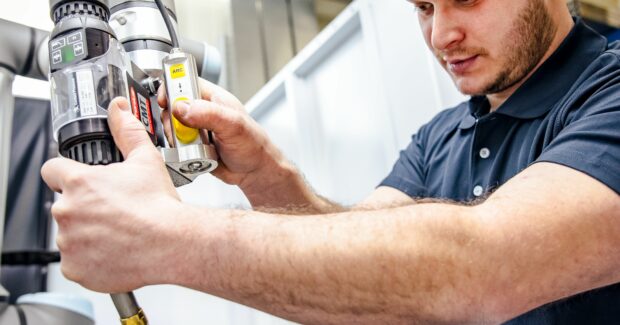
The future for cobots is exciting. There are developments on further improvements with usability and programming that implement artificial intelligence.
Sheet Cutting Lasers and the Great Decision
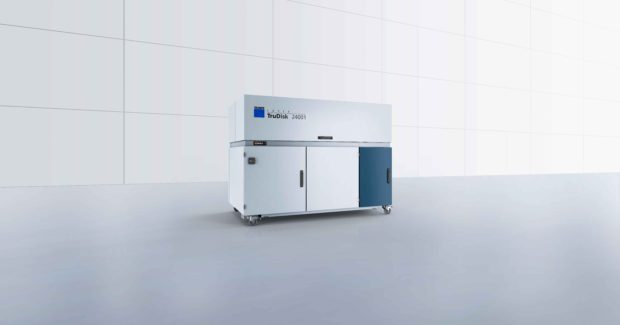
At the end of the day, the decision about laser power, like any good investment decision, should be based on profitability.
The Big Benefits of Small Hand Tools
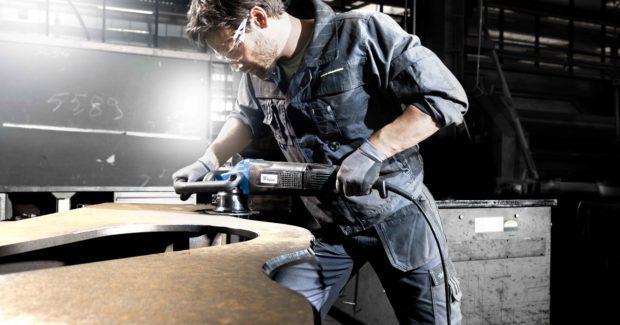
These small but powerful machines help small fabrication shops leverage their workforce to be more productive, and they complement the big, advanced production systems found in more automated factories.
Introducing Clean Tube Laser Processing
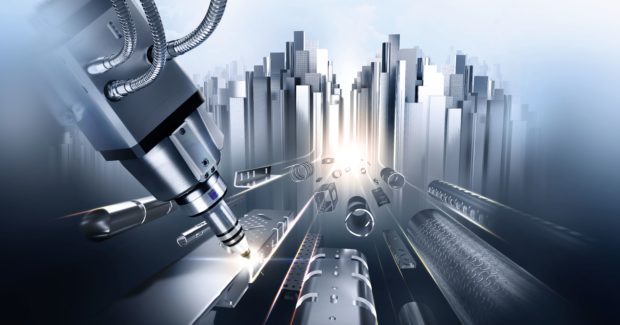
Automatic spatter protection represents a significant increase in productivity when utilizing tube laser cutting lines.
Mixed-gas Laser Cutting Opens up Possibilities for Thick Steel Fabrication
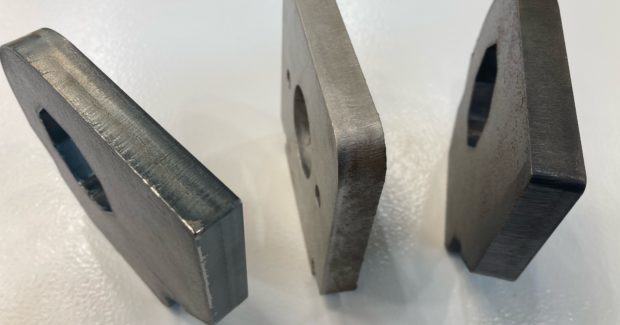
Laser cutting with pre-mixed assist gas has been gaining traction as a fair compromise between cutting with oxygen and increasing the laser power output.
Nano-joints Offer Enormous Potential in Laser-Cutting Processes
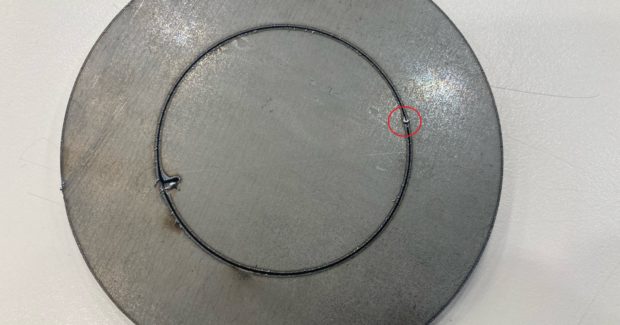
Nano-joint technology allows fabricators to keep small parts securely attached to the nest without a hard tab that is difficult to break or requires clean up.
Bending the Rules: Press Brake Technology Helps Turn New Operators into Forming Experts
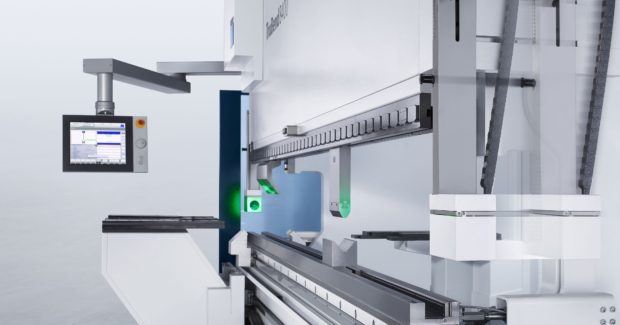
Innovations in press technology are pushing down the barriers for new operators to learn metal forming and making the process of training new operators safer and more productive.
Another Dimension to Flat Sheet Laser Cutting
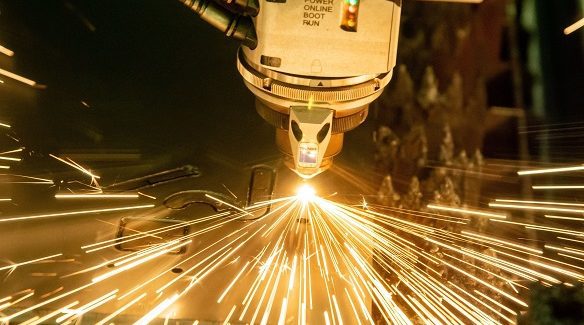
The ability to perform edge contouring on flat sheet cutting lasers makes laser cutting even more flexible as a fabrication tool.
Meet Dot Matrix: A Basic Tool of Industry 4.0
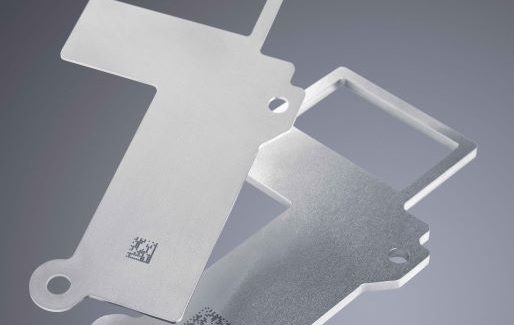
From the factory of origin to the final destination, dot-matrix codes can help track, trace and inform everyone in the product lifecycle. The dot-matrix code really is one of the most basic, and important, tools of Industry 4.0.
Modern Punching Technology Makes Complex Sheet Metal Processing Easy and Attractive
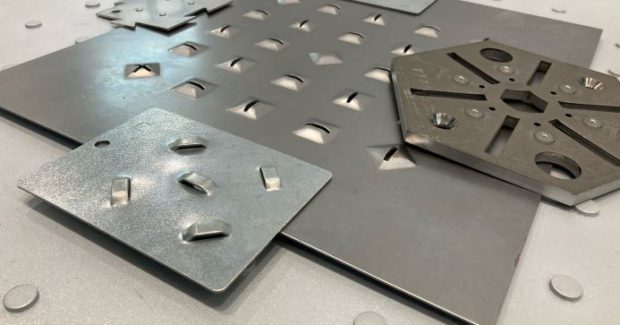
The punch as a metal working tool offers overlooked advantages, including supporting and enhancing traceability in a sheet metal product.
Data Driven Production, from Order Entry to Execution
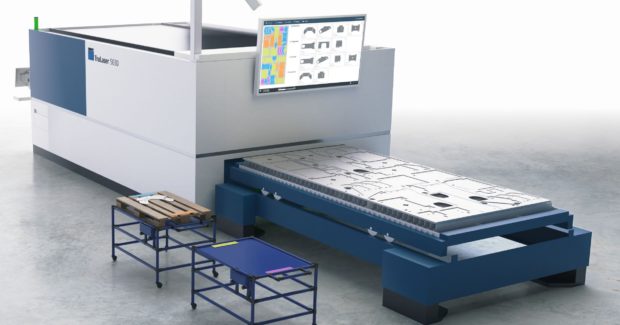
Break data into small segments in order to develop good data, resulting in better solutions.
When (and How) to Automate Sheet Metal Welding
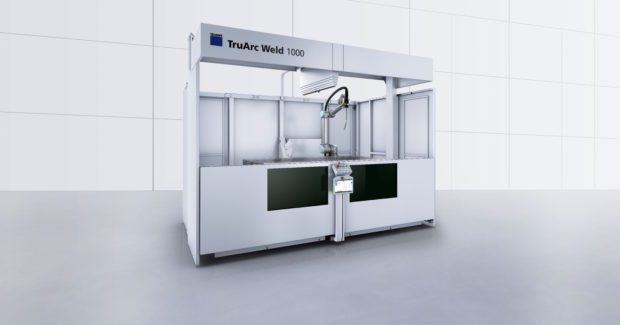
Cobotic welding systems occupy the gap between fast and heavy industrial robots and manual welding. They also challenge the paradigm that welding automation is strictly a high-volume game.
How to Get the Most Out of Today’s Sheet Metal Laser Cutters
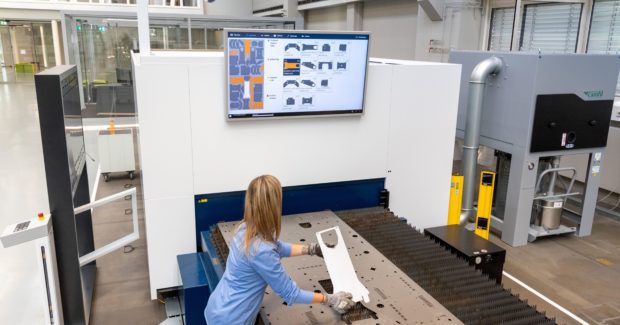
There’s a big difference between just cutting fast and achieving impressive throughput. As machines become faster, factories must properly manage downstream handling processes.
Totally Tubular: Take Profile Design to the Next Level
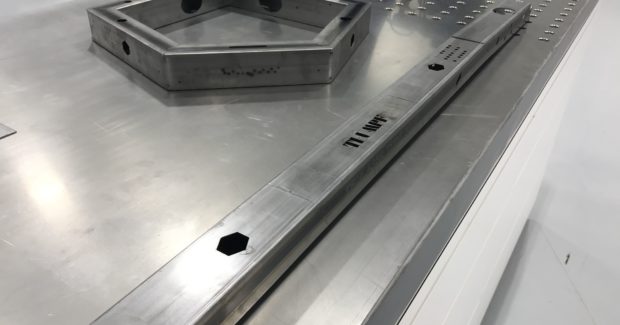
One of the fastest-growing sectors of North American metal manufacturing is laser processing of tubes and profiles. Design software and machines that automatically perform multiple manufacturing steps are making this complicated fabrication process cost-effective for smaller companies.
Laser Cutter That Thinks for Itself Opens the Door to a Fully Automated Process
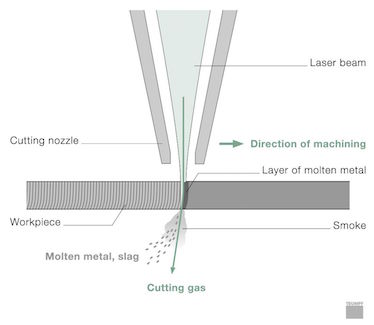
Trumpf’s Active Speed Control uses artificial intelligence to completely eliminate the need for an operator to monitor cutting and, if necessary, tweak parameters. The technology automatically adjusts feed rate to ensure part quality when cutting plate with chemistry, thickness, or surface condition variations.
The Practical Impact of Industry 4.0 – Part Three: Connecting the Dots
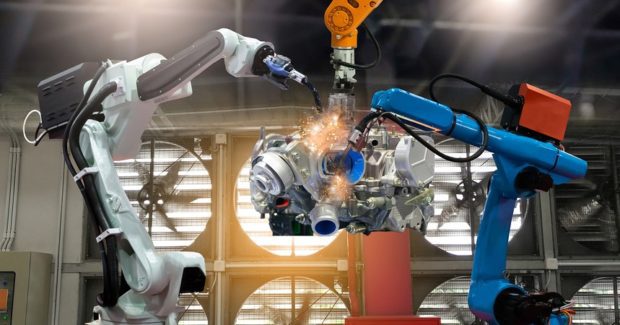
Building the Smart Factory starts with digital processes and automated machines, but it ends with intelligent connections between resources and tasks. Linking together people, machines and software inside a plant enhances the capabilities of each and creates a system that is more valuable than the sum of its parts.
The Practical Impact of Industry 4.0 – Part 2: Automatic Manufacturing
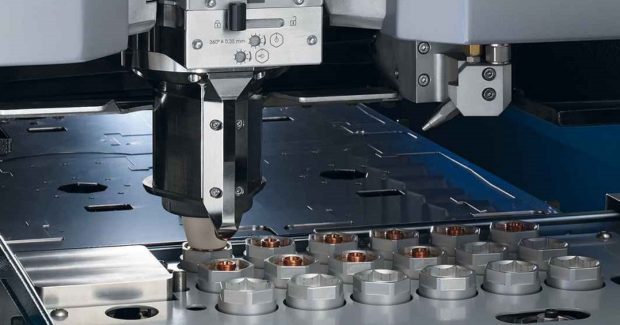
Last time we saw how Industry 4.0 uses automated software to control and simplify the flow of information and tasks. Now let’s explore how it uses automated hardware to control and simplify the flow of materials and goods.
The Practical Impact of Industry 4.0 – Part 1: The Digitalization of Processes
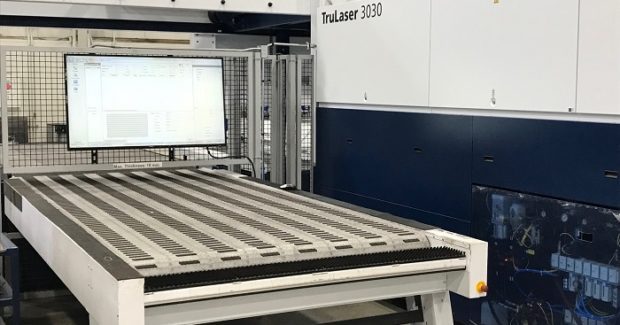
Anytime you must “go and see” something that could be transmitted electronically is an opportunity to connect. Anytime you read data from one place and copy or send it to another is an opportunity to automate. And here’s the great thing: If you are just starting out, it’s pretty easy to take small steps.
More Than One Way to Skin a Part: Where Fabrication and Machining Overlap
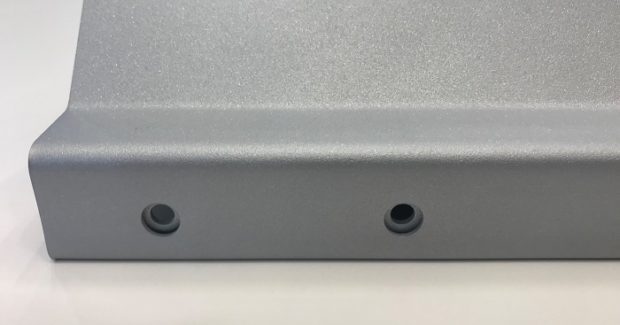
Don’t take the “hard limits” between machining and fabrication for granted. Their areas of overlap offer tremendous potential for savings. If you manufacture parts using both processes, take a second look at some of them to evaluate whether they could be produced more economically with a little sheet metal know-how and some outside-the-box thinking.
Technical Service in the Era of Industry 4.0
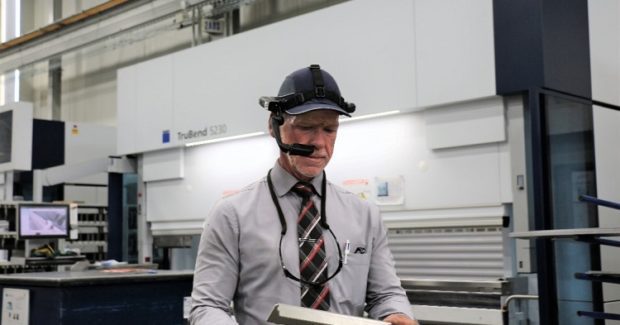
As machine tool manufacturers work on enabling technology to make the Smart Factory possible, the field of machine service and support has started to drastically minimize the window of lost productive time that shops must deal with.
May the Press Force Be with You: Tips and Tricks for High Tonnage Bending
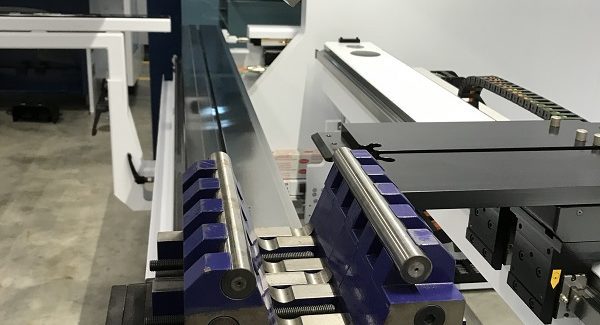
Bending thick plates requires more attention to certain details than lighter bending jobs. Here are some ways to get all your ducks in a row before you bend the first part, so that your job will go more smoothly and translate into more profitable production.
Sheet Metal Marking Review
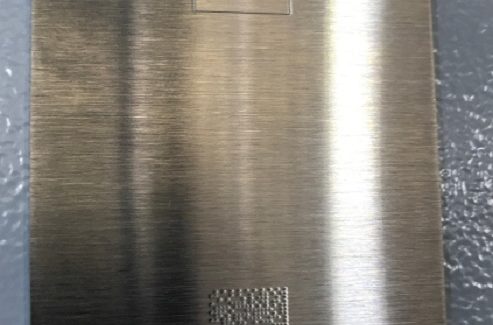
Demands are growing for sheet metal fabricators to mark their parts during production for product traceability in the field and better efficiencies in the shop, but many part identification systems can add an unnecessary secondary process. Whenever possible, consider finding ways to incorporate part marking into a manufacturing step that is already required. Here are some ways to use the equipment that you already have.
Keeping it Cool: Why Machines Depend on Chillers, and Chillers Depend on You

Lax water maintenance has a huge potential downside in laser cutting machines: bad water could lead to extreme overheating and complete failure of the laser. Here are some other reasons why keeping cool and remembering to change the chiller water will get the most work out of your machinery at the lowest cost of ownership.
Built to Last: Sheet Metal Design with Strength in Mind
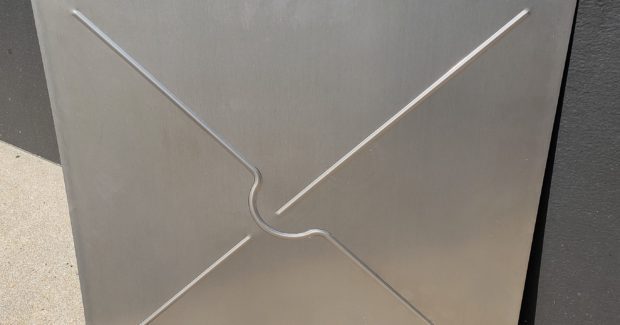
Sheet metal has a high strength-to-weight ratio and good malleability that can provide form and structure to products, but because it is flat and bends easily, it doesn’t always work. Here are some ways to increase the structural strength of flat sheet stock without adding gussets or increasing the weight of the product.
Beyond Bending: Press Brakes Can Do Much More
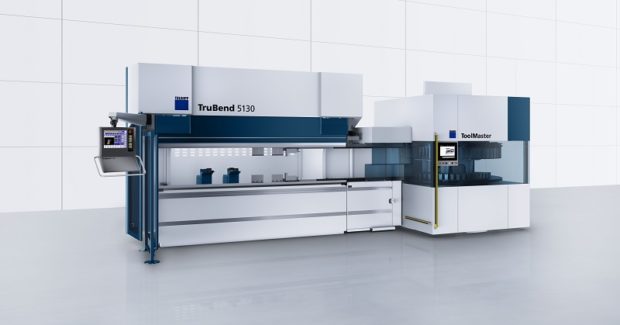
It might come as a surprise that the press brake you walk by on the shop floor each day can do a lot more than make flanges. When considering how to get from product drawings to finished goods, keep in mind that your press brake can do so much more than just bend.
Advanced Metal Joining with Laser Welding
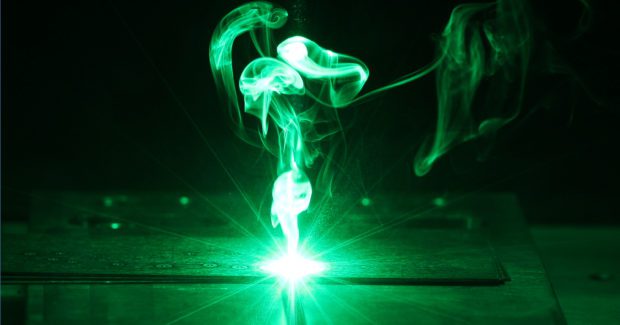
Laser welding is becoming more common to a wider audience that is discovering how its unique properties can create stronger and more aesthetic weld seams than conventional GMAW processes, and how it can tackle weld geometries that were once impractical or downright impossible.
Cut-to-Break: Optimizing Punching Operations for a Superior Edge
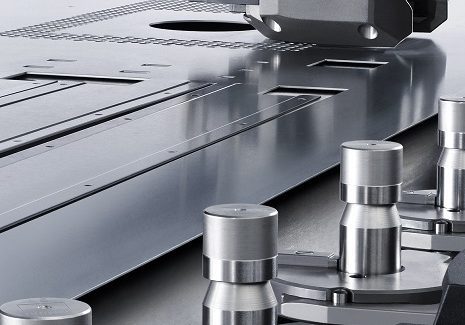
When it comes to flexible sheet metal fabrication, the punch machine might be a very old dog, but it has shown time and again that it has no problem learning new tricks with modular and interchangeable tooling.
Laying Groundwork for Great Laser Cutting: Start with the Slats
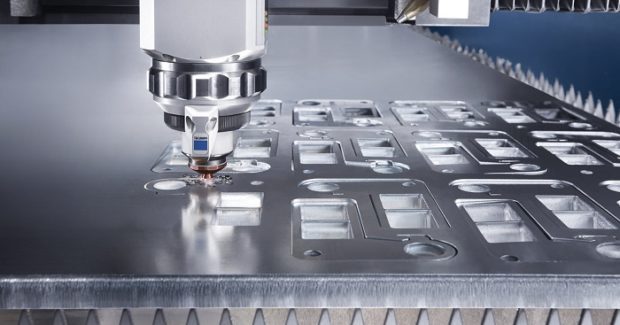
Though it is often overlooked by equipment users, one of the most critical factors to consistent laser cutting quality is the proper maintenance of the worktable where the cutting process takes place.
Productive Meets Safe: Equipment Enhancements that Help Prevent Press Brake Injuries
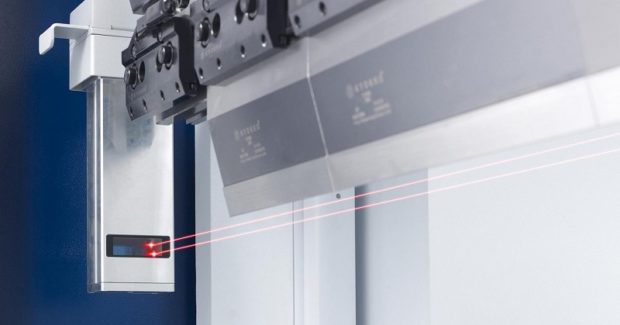
Unless they are fully automated, production on CNC press brakes cannot occur without an operator’s hands being constantly in near proximity to a potential danger zone. For this reason, increasing efforts are being directed toward fail-safe measures on these machines. Here are some of the latest improvements that have been developed by press brake manufacturers to reduce the likelihood of accidental injuries.
The King of Cutting Sheet Metal Up to One Inch Thick
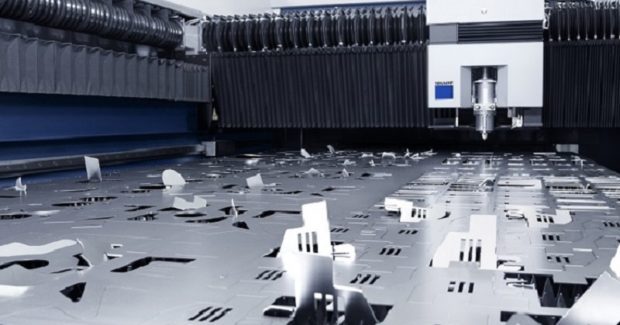
When jobs call for cutting sheet metal in thicknesses around one inch and under, waterjet and plasma cutting pale in comparison to laser cutting. Here are the reasons why it is the clear front runner for shops that compete in this type of work.
Make Your Mark
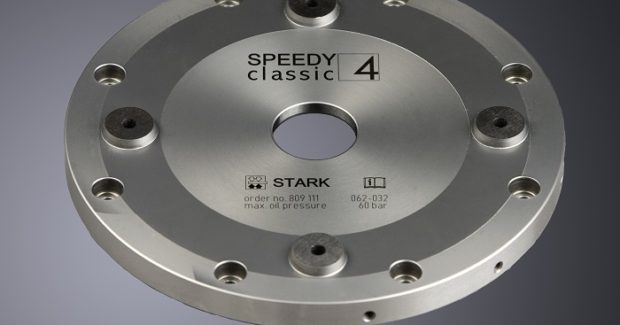
Whether you mark your parts for identification, ornamentation or post processing, there are several options to consider. Regardless of the purpose of the mark or the material to be marked, there is a product marking system to fulfill your needs. Here are several different ways for you to make your mark.
Closing the Loop: Strategies for Bending Closed Forms
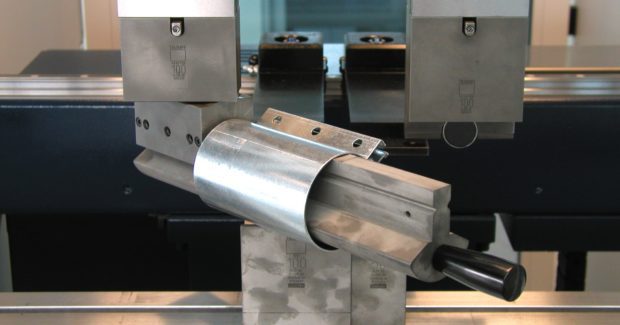
With a bit of creativity and thought to overcome limitations, it is often possible to form closed profiles and other difficult parts with a standard press brake. Here are some tips on how to do it.
A Little TLC Means a Lot to Press Brake Tooling
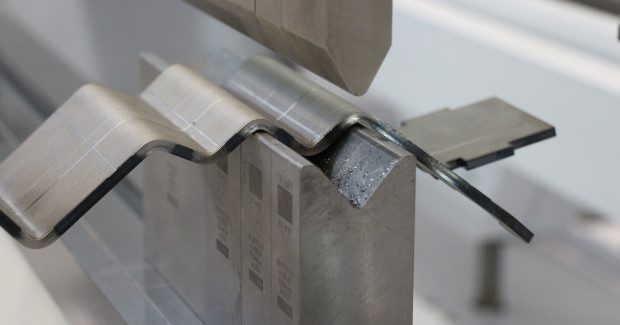
Press brake tools are the only parts of the machine that ever touch the finished parts being formed. The best precision CNC press brake cannot produce good products with poor tooling, and bad tooling makes all the good hardware in the process – including the machine operator – useless.
A Practical Approach to Bending Length Precision

To hit those very small flange length tolerances on our prints, we need to master that material stretch. This means we need to understand not just the material, but also how the press brake tooling being used to perform the bend will change the amount of stretch and impact the size of the blank.
Breaking Down Automated Bending
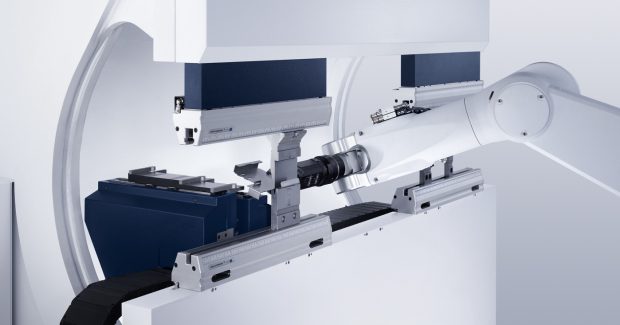
Here are five basic areas to evaluate when considering whether it is right to invest in an automated bending solution, and if so, which type of system to choose.
Rethinking Bending Automation
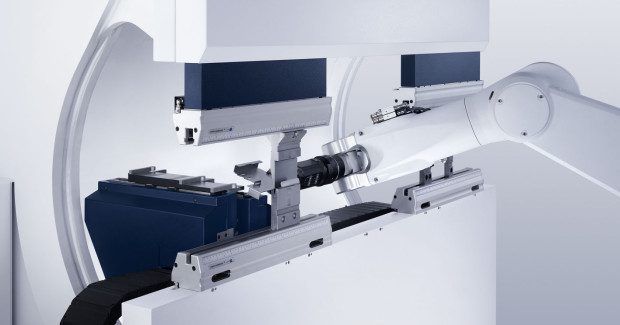
Don’t attempt to adapt an assembly robot into a bending cell. New application-driven robots work alongside press brakes to simplify part programming and minimize cycle times. Instead, add process reliability enhancements and offline software and your return on investment for bending automation becomes clear and highly achievable. Here’s how to do it.
Bending Aesthetics: When the Finish Comes First

Sometimes marks caused by the lower die during the bending process can turn a good part into scrap metal, even if the scrapes are very light and have no functional bearing on the part whatsoever. To deal with this problem, it is necessary to reduce or eliminate the movement of the material over the hard shoulders of the die. Here are several ways to do this.
GOING FOR GREEN LIGHT: REDUCING LASER SETUP TIMES TO KEEP THE BEAM ON
Green light time is the way to make money operating a machine tool, and it never hurts to go back and review some basic principles for improving productivity in a laser fabricating process. With an eye toward keeping that light on longer, Tom Bailey of Trumpf looks at a few simple strategies that can pay off.