Welding
Filter by Process Zone:
THE WORLD IS NOT FLAT: TIPS TO IMPROVE OUT-OF-POSITION WELDING (Part Two: Stick Welding)
Fabricators often need to weld out-of-position when working with large/heavy weldments and with pipe, which requires adjusting the electrode angle, puddle manipulation, body position and equipment settings. In the conclusion of this two-part series, Ken Alrick of Thermadyne focuses on stick welding mechanics and shows operators the variables that can help them control weld puddle and weld bead profile.
TIG TORCH IMPROVES WELDING PERFORMANCE AND CONTROL ON MULTIPLE MATERIAL THICKNESSES
Ideal for professional or hobbyist welders, these six different TIG torches from Weldcraft, including some with gas valves and flex necks, provide 150 amp DC and 115 amp AC welding capabilities at 60 percent duty cycle and are available with 12.5 ft and 25 ft, one-piece or two-piece cable lengths.
UNIQUE MIG GUN SYSTEM DOUBLES PRODUCT LIFE, REDUCES COSTS
The Double-Life MIG Gun System from Tregaskiss operates at cooler temperatures to minimize downtime and cost for changeover and replacements, and a full-length liner can be installed from the front end of the MIG gun in less than half the time of a conventional liner replacement to further reduce costs.
NO TURNING BACK:
PIPE WELDING SYSTEM KICKS IT UP A NOTCH
Using the PipeworxTM Welding System from Miller Electric, Shinn Mechanical has increased its pipe fabrication quality and productivity with flatter bead profiles, good sidewall tie-in for 30 percent less grinding, and superior weld puddle control – with no wire rejects in over a year.
UP TO THE TEST
This eye-opening case study explores how Arizona handrail fabricator Hot Az Hell Welding and Fabrication put their welding guns from Bernard to extreme tests during an upgrade from stick to the flux-cored process.
THE WORLD IS NOT FLAT: TIPS TO IMPROVE OUT-OF-POSITION WELDING (Part One)
Fabricators often need to weld out-of-position when working with large/heavy weldments and with pipe, which requires adjusting the electrode angle, puddle manipulation, body position and equipment settings. The first in this two-part series by Ken Alrick of Thermadyne takes beginning TIG knowledge to an intermediate/advanced level by comparing right and wrong methods of making these adjustments.
REAMER QUICKLY CLEANS AND REMOVES SPATTER FROM THE MIG WELDING NOZZLE
The Tough Gun Reamer from Tregaskiss reduces automated MIG welding expense, speeds set-up and lowers downtime by quickly cleaning and removing spatter.
ALL-IN-ONE WORKSTATION FOR WELDING AND METALWORKING
An affordable workbench from Miller Electric designed specifically for welders has customizable options that make it the ideal welding workbench for both the fab shop and the home shop.
PORTABLE PLASMA CUTTING FOR ON-SITE CONSTRUCTION
Designed for cutting mild steel, stainless steel, aluminum, brass and copper, Tomahawk plasma cutting systems from Lincoln Electric are ideal for on-site maintenance, service tasks, small construction sites, HVAC work, demolition and rental applications.
FLUX-CORED WIRE IMPROVES WELDING QUALITY ON HIGH-STRENGTH STEEL
This wire from Hobart Brothers provides excellent low temperature impact toughness, is ideal for offshore and structural applications, and offers 100 – 110 ksi tensile strength.
MIG WELDING CONSUMABLES REDUCE DOWNTIME IN HIGH HEAT APPLICATIONS
These consumables from Bernard also have a spatter guard improves shielding gas coverage, reduces diffuser wear and “drop in” contact tips change quickly and without tools, all to deliver superior performance.
10 Common TIG Problems and Solutions
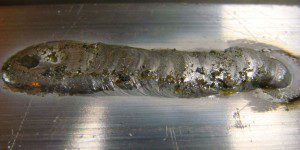
Here are some descriptions of common TIG mistakes and basic tips on how to prevent these errors from happening.