Tooling & Workholding
Filter by Process Zone:
Modular Die Cushion System Extends the Life of Deep-Drawing Dies

The Modular Die Cushion System from Moog improves process reliability, reduces commissioning time, offers flexible layout options for integrating the manifold and requires comparatively little piping to help press rooms lower their maintenance and piping costs.
Online Equipment Monitoring Drives Productivity Improvements
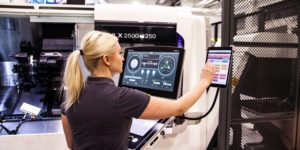
The CoroPlus MachiningInsights digital system from Sandvik Coromant collects data directly from a connected machine tool and input from operators, making it possible to visualize machine and tool utilization levels online through a web browser and collaborate to make improvements within the factory.
Tool Measuring Systems and RFID Working: A Powerful Combination
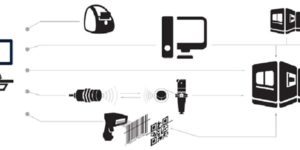
Efficiently moving information around your shop floor is more important than ever. Connected through RFID, a shop can now use a tool presetter to monitor things never monitored before and use that data to fine-tune processes, reduce inefficient costs like scrap and waste, and make the factory floor smarter, streamlined, far more efficient and competitive.
Prevent Slug Pulling with the Right Die Clearance
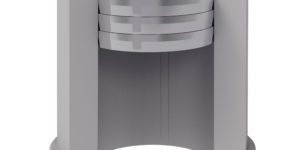
Proper die clearance allows for upper and lower fracture lines to connect. The typical stamping industry rule of thumb is to use 10 percent material thickness as clearance between the punch and die button, but this guideline does not take into account variable material types. What is the optimal die clearance?
How to Clean Welds Faster With a Wire Brush
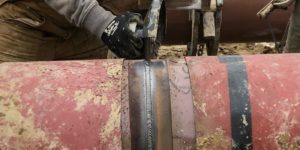
Saving even a few minutes with each weld cleaning can add up over time in the welding operation. Here’s how to choose the right wheel for the job and the best practices to follow that will optimize performance and efficiency when using wire brushes.
Meeting the Challenges of Sawing Exotic Materials
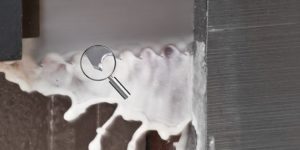
Are you having problems with these tough materials? New and better blades are increasing blade productivity while maintaining or improving both blade life and cut tolerance – they are even being used to cut parts to a final size, without the necessity of additional machining.
First Automated Tool Changer Certified in Americas for UR+ Program

Universal Robots certifies the QC-11 Automated Tool Changer from ATI as the first automated tool changer developed in Americas for the UR+ platform to work seamlessly with UR cobots.
Weiler Abrasives Achieves Milestone
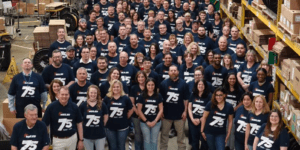
They are celebrating 75 years in business.
ATA Acquires Karnasch
This deal expands the international cutting tool business of ATA.
Absolute Machine Partners with Sussex Tool & Supply
This deal gives Absolute better proximity to customers in both Wisconsin and Illinois.