Stamping Presses
Filter by Process Zone:
Tenneco Installs New Lubrication Equipment
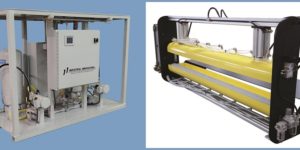
The two lubrication systems from Industrial Innovations are used in the pressroom of their Elkhart, IN, automotive plant.
Majestic Industries Achieves IATF Certification
They are certified for Automotive Quality Management System IATF 16949 for producing metal stampings and stamping dies.
Egar Tool & Die Installs New Lube Application Systems
The high-pressure Spra-Rite systems from Industrial Innovations are used in their stamping and drawing operations.
Industrial Innovations Expands Sales Network
Die Maker Solutions now represents their lubrication systems for metal stamping and forming shops in Texas and Oklahoma.
Moving Toward the Smart Press Shop
Schuler and Porsche form a joint venture to build an innovative press shop for the car factory of the future.
Electronic Tapping Units Increase Stamping Productivity
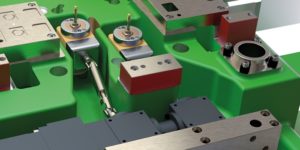
Electronic Tapping Units from Fibro incorporate advanced servo technology and process control to increase stamping productivity and efficiency with a thread range of M0.8 to M24 and production speeds exceeding 140 SPM.
Servo Presses Increase Productivity, Improve Part Quality in Near-Fine Blanking and HSLA Blanking
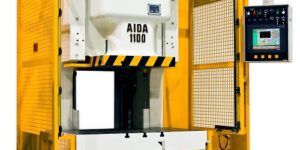
The DSF-C1-1100 110 ton gap frame servo press and DSF-N2-3000 300 ton two-point straightside servo press from AIDA-America provide more flexibility to the press room than traditional fine blanking presses and a much more efficient, economical stamping process.
Coil Lubricating System for Stamping Improves Accuracy and Reduces Costs
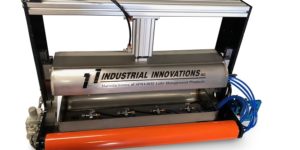
The Spra-Rite UltraCoat non-contact spray system from Industrial Innovations is designed for easy coil feed installation and press control communication for reliable, economical application of lubricant to stock prior to stamping to help improve accuracy and reduce overspray and consumption.
Wireless Pressure Monitoring of Nitrogen Gas Springs and Systems

Through 24-hour monitoring and documentation, the Wireless Pressure Monitoring system from Fibro achieves zero defects and prevents scrap for production stampers due to the loss of nitrogen gas spring or system pressure.
Beckwood Builds Compression Molding Press for U.S. Army
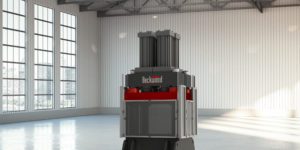
The custom 1,000 ton hydraulic press will be used to consolidate ballistic composites.
An Overlooked Way to Keep Up with Industry Change
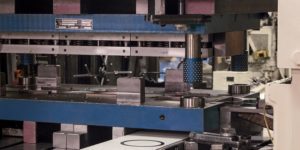
Press operation requirements, inspection needs, improved die technology, tool room utilization and lean initiatives are all transforming the way shops compete. But what if you can’t keep the die in the press because of cheap tooling?
Automotive Manufacturer Boosts Production with Custom Transfer Tooling
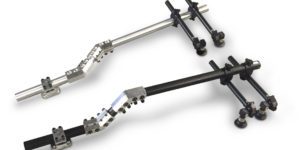
To reduce weight for lower deflection, Toyota Motor Manufacturing of Canada uses Accelerate Lightweight Tooling from Destaco for higher precision, reduced scrap and improved operational efficiency on their stamping press.