Punches and Dies
Filter by Process Zone:
How to Increase Productivity and Efficiency in Production Stamping

The Fibro Electronic Tapping Unit and the Wireless Pressure Monitoring from Fibro enables production stampers to add value, increase throughput and improve operational efficiency.
In-Die Tapping of AHSS Material and More
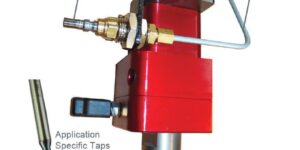
Jarvis Cutting Tools works directly with machine builders to develop exclusive high-performance taps that address current and future production requirements.
Mechanical and Servo Style In-Die Tapping Heads
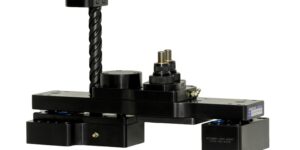
In-die tapping head technology from Hutchison Tool provides a tapping range from #2-56 to 1-1/4-12 or metric M2 to M30 that run in press strokes from 3 in to 20 in.
How to Eliminate the Need for Spot Welding and Riveting

One simple, high-cycle punch and die operation automatically feeds, punches, inserts and locks the self-piercing FAS-NER from AKH to produce a solid joint in similar or dissimilar metals and thicknesses.
Single Source Capabilities for Die Design Through Manufacturing
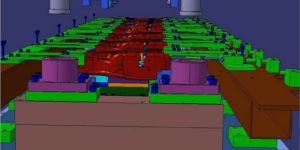
Tooling Tech Group is a single source supplier of everything from die design, simulation and engineering through to die build, repair, try-out and production stampings.
Spring Force Wedge Clamps Allow Clamping Without Permanent Hydraulics
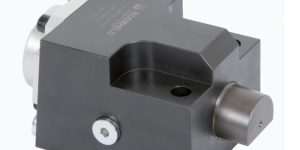
Hilma self-locking wedge clamps from Carr Lane Roemheld are powered by spring force that is ideal for clamping dies with a straight clamping edge, for metal stamping die change or plastic mold change.
Roll-Kraft Adds CFO
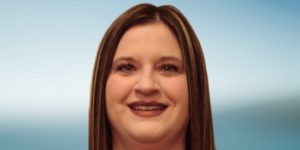
Jacqueline Kato is their new chief financial officer.
Stamping AHSS Got You Down? Reconsider Your Tool Design
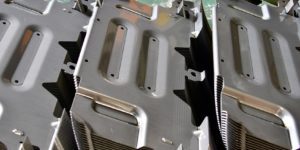
To reduce wear and tool breakage when forming or blanking AHSS material, here are some tips on revisiting the type of tool steel used, the design of the tool itself, and whether or not adding a coating or surface finish will improve performance and provide longer tool life.
Stay Sharp for Maximum Tool Life

To prevent lower quality parts and frequent tool replacement, keep your punch press tooling sharp and well maintained to achieve the greatest number of hits possible for the best possible return on your investment.
Tooling Tech Appoints New Officer
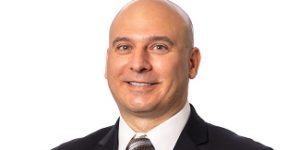
Todd Wodzinski is their new chief commercial officer.
Modular Die Cushion System Extends the Life of Deep-Drawing Dies

The Modular Die Cushion System from Moog improves process reliability, reduces commissioning time, offers flexible layout options for integrating the manifold and requires comparatively little piping to help press rooms lower their maintenance and piping costs.
Prevent Slug Pulling with the Right Die Clearance
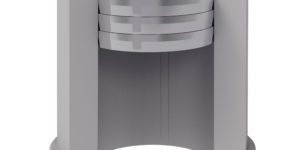
Proper die clearance allows for upper and lower fracture lines to connect. The typical stamping industry rule of thumb is to use 10 percent material thickness as clearance between the punch and die button, but this guideline does not take into account variable material types. What is the optimal die clearance?