Punch Presses
Filter by Process Zone:
Metcam Wins Awards
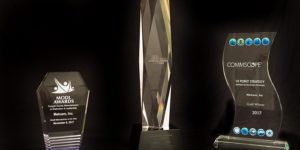
They have won three best company awards in five months, including top honors in the state of Georgia.
Industry 4.0 Machinery for Smart Factory Operations
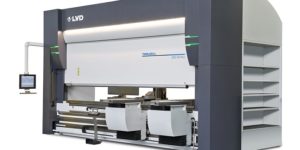
ToolCell press brakes from LVD Strippit use the Easy-Form Laser adaptive bending system for in-process angle monitoring via laser scanners located on the front and back of the press brake table.
All-Electric, Servo Powered Presses for Automated Cells
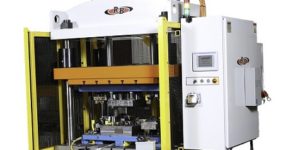
With the capability to load dies from the front or back of the machine, these presses from R&B Machining utilize robust machine actuators that balance precision positioning with speed and provide cost effective screw life.
Economical Ironworkers and Punch Presses for Full Fabrication of Standard and Custom Jobs
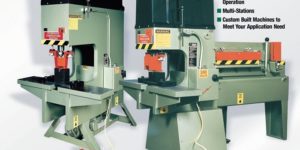
The two-cylinder/two-person operation of the MM Series Complete Five-Station Fabrication Center from Kalamazoo Metal Muncher allows the punch and shear end to be operated separately, independently and simultaneously at full capacity and speed. Their GB Series Hydraulic Punch Press can also be fitted with special tooling to allow shearing or forming.
The ROI Threshold
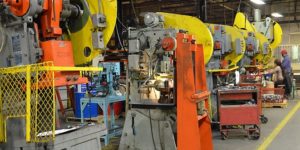
What happens when demand for parts from a supplier increases so that an OEM can scale up production? Determining the ideal time to transition to a more economical alternative can be challenging, but a “one-stop” parts supplier can scale with demand, facilitating the transition to hard tooling, mixing and matching metalworking techniques for multi-component assemblies, and incorporating hybrid and secondary tooling approaches to further reduce costs.
Waukesha Metal Products Invests in Fiber Laser Technology
They install a 4 kW fiber laser cutting system in their fabrication facility in Grafton, WI.
Beckwood Engineers Two Servo-Driven Electro-Mechanical Presses
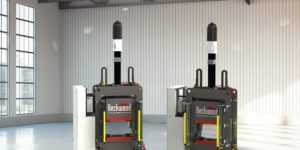
These two 13 ton presses will be used by a leading footwear manufacturer in a trimming application.
Beckwood Press Expands Engineering Capabilities
They add five engineers and one drafter to meet the exceedingly sophisticated demands of their evolving customer base.
Beckwood Press to Relocate Headquarters
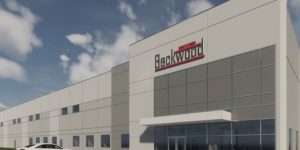
The new 55,000 sq ft state-of-the-art facility will be less than one mile north of their current location.
Deep Draw Hydraulic Press System Run by Robots
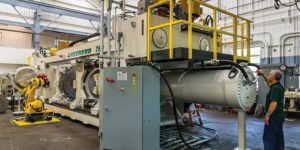
To perform the multiple operations required to produce a heavy duty high pressure cylinder tank, a 750 ton deep draw hydraulic press from Greenerd Press uses a double-moving platen that is fully integrated with two 6-Axis FANUC robots that load/unload parts and prompt the press to cycle for operations.
Virtual Press Design Technology Takes Center Stage
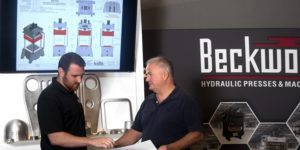
Using virtual press design technology via a user-friendly interface, customers can work with Beckwood Press engineers to input a variety of variables (bed size, tonnage, speed, heat parameters, etc.) and generate a preliminary sketch of new machinery that meets their specific application requirements.
Greenerd Partners with FANUC as Tier 1 Authorized Robot System Integrator
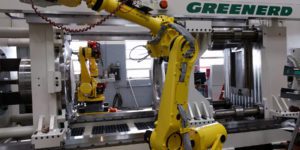
To provide advanced automation systems in short time frames, Greenerd now has full access to all FANUC Robot models, training and support.