Filler Metals/Electrodes
Filter by Process Zone:
Considerations When Selecting a Filler Metal (Part One)
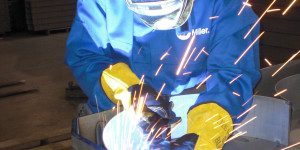
Filler metal selection is critical to maintain the integrity of the final weldment. Here is a review of their general properties that can help you determine which filler metal is ideal for the job.
Tips to Make Welding Operations More Profitable
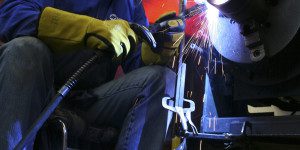
These tips may involve an investment of time, effort and resources, but they can pay off in the long run for welding operations that use a variety of welding processes and equipment.
New Filler Metals
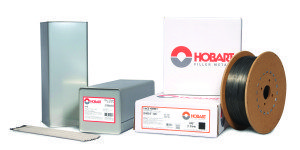
The latest flux-cored wires, metal-cored wires and aluminum filler metals from Hobart Brothers are designed to improve quality and productivity in welding operations.
Gaining Efficiencies by Increasing Welding Wire Size
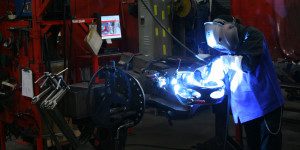
The time and energy it takes to make the conversion from smaller-diameter wire to a larger one could save countless hours and improve quality. Here are several initial steps that are necessary to make the conversion.
Tips for Taking the Trouble Out of Aluminum Welding
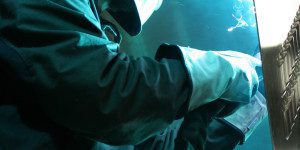
Here are some tips on how to maintain exceptional cleanliness, select the right filler metal and employ the correct welding preparations to remove the oxide layer on the surface of the material.
Aluminum Welding Wire for Heavy Duty Applications
SuperGlaze HD aluminum welding wire is perfect for use in heavy-duty applications where wire feeding can be a challenge and arc performance is critical.
What You Must Know About Filler Metals
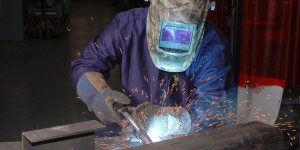
Understanding these important details will help your shop decide whether a new welding technology is your best way to remain competitive or if a filler metal conversion your best next step.
What’s New with Filler Metals?
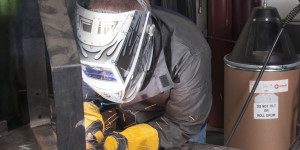
Filler metals reflect how welding operations are evolving, as materials change to meet application demands that require technologies capable of meeting more specific — and sometimes more stringent — welding requirements.
Filler Metals
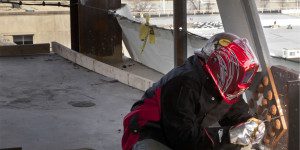
A snapshot of some of the newest filler metals used in welding applications.
Filler Metals: Accuracy in Ordering and Usage Matter
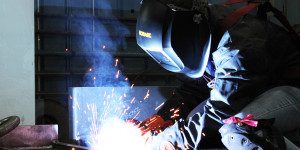
It only makes up about 20 percent of the cost of your typical welding operation, but incorrectly estimating the amount of filler metal needed can have a far-reaching impact to your bottom line.
Common Causes and Cures of Hydrogen Cracking
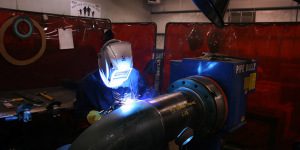
Knowing the means by which hydrogen can enter the weld is a good defense against potential problems. These steps can help reduce the risk of cracking that leads to costly rework, downtime, increased labor needs, poor productivity and most importantly, product failure.
Welding Wire Meets Manganese Exposure Limits
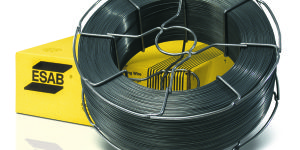
Coreweld C6 LF low manganese emission metal-cored welding wire from ESAB is ideal for hand held or automated welding in automotive, civil construction, mobile and heavy equipment, shipbuilding, rail car manufacturing and general fabrication.