Computerized Maintenance Management Systems
Filter by Process Zone:
Economical Process Monitoring of Metal Forming and Stamping Operations
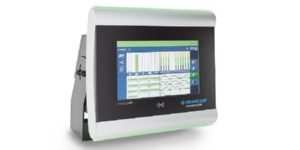
The intelligent Brankamp X3S real-time process monitoring system from Marposs immediately identifies manufacturing faults and part or tool variations to optimize machine efficiency, improve part quality, and limit unplanned downtime and tooling costs.
A World Without Downtime
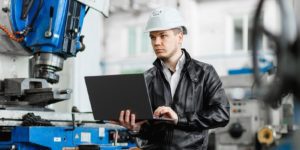
While 70 percent of manufacturers lack full awareness of when their equipment is due for maintenance, upgrade or repair, does it have to be this way? Is abolishing unplanned downtime in Industry 4.0 a far-fetched dream, or is data-driven maintenance closer than we think?
Destination: Utopia

As Industry 4.0 connects more sensors, combines digital twins with machine learning software and expands the use of data-driven automation, the continual reduction of downtime will slowly move manufacturers toward the promise of paradise.
Added Value: The Importance of Aftermarket Care
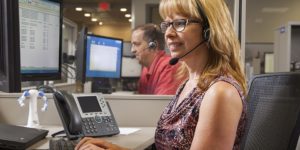
You’ve covered every detail in upfront costs and factory floorspace, but what about technical support and service after production starts? Whether buying one robot or hundreds, having access to diverse support services to ensure peak robot performance is vital to maximizing your return on investment. Here’s why.
Smart Proximity Sensors Improve Predictive Maintenance

E2E NEXT proximity sensors from Omron feature exceptionally long sensing distances and IoT functionality that helps shops reduce potential causes of unplanned downtime.
Perpetual Wireless Equipment Health Monitoring

The Vero equipment monitoring system from Nikola Labs promises to simplify maintenance and perpetually power sensors without wires or disposable batteries.
The Future of Industrial Hydraulics

Achieving energy savings up to 60 percent in medium performance applications up to 30 kW, the compact CytroBox hydraulic power unit from Bosch Rexroth integrates IoT technologies for connectivity, condition monitoring, data analysis and more.
Predictive Monitoring Moves to The Next Level
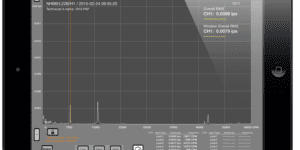
VibePro 24/7 online vibration and temperature monitoring technology from GTI improves data collection for rotating equipment and bearing health, allows users to easily change assets from route collection to online data collection, clones machines, points and plant areas, and generates long-time waveform for ultrasound display.
Spindle Diagnostics: Predictive Maintenance at Your Service
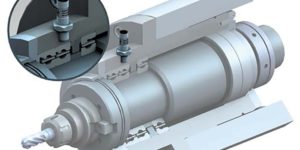
Installed directly into the spindle, the miniaturized B-Safe system from Diamond Industrial Tools uses vibration and temperature analysis for real-time monitoring of anomalies, predicting malfunctions and reducing machine downtime.
AI-Driven Remote Machine Monitoring
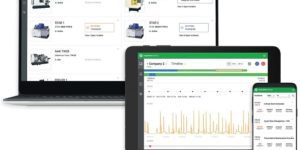
Using the Service predictive analytics application from MachineMetrics, OEMs and equipment distributors can transform their approach to service with the ability to see, understand and take action on their customer’s real-time machine data from anywhere at any time.
How to Use Virtual and Augmented Reality in Manufacturing
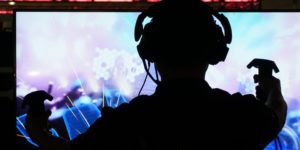
How simulating the factory can help fix mistakes and improve production.
Technical Service in the Era of Industry 4.0
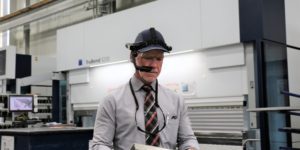
As machine tool manufacturers work on enabling technology to make the Smart Factory possible, the field of machine service and support has started to drastically minimize the window of lost productive time that shops must deal with.