Versatile Turning Center Solutions Ensure Your Shop Stays Competitive
Innovations in turning centers and lathes reduce set up times allowing you to produce more complex parts in shorter time frames.
Posted: November 16, 2024
Multi-tasking capabilities, automation and other improvements result in efficiency, flexibility and precision machining when it comes to the next generation of turning centers and lathes.
Latest Generation of Multi-Spindle Lathe Increases Flexibility and Efficiency
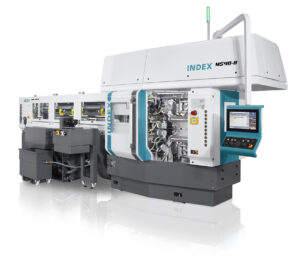
The latest generation of the INDEX (Noblesville, IN) MS40-8 multi-spindle automatic lathe made its North American debut at IMTS 2024. This newest version of the company’s popular eight spindle machine incorporates a variety of features that reduce setup and changeover times while also enhancing flexibility.
Accommodating bar stock up to 40 mm in diameter, the MS40-8 provides up to 16 tool carriers, which can be configured with X, Y and Z axes. Tool carriers can optionally be equipped with C and Y axes, as well as live tools. This enables a wide range of metal cutting applications, including off-center drilling and threading, inclined boring, cross drilling, contour milling, gear hobbing and polygonal turning.
The machine can be equipped with one or two swiveling synchronous spindles for back working, each of which is served by up to seven tools, with four spots for live tooling. This customizable approach allows the MS40-8 to be operated as a double four-spindle machine for the fastest possible production of low-complexity parts, or in various configurations that can be optimized for parts of higher complexity.
INDEX’s patented W-serration interface and quick clamping system are included on the MS40-8. This unique system streamlines tool setups and changeovers while maintaining high repeatability and accuracy. The machine also incorporates INDEX’s compact spindle drum and three-piece Hirth coupling that ensure maximum rigidity and precision. Each of the machine’s eight spindles can simultaneously operate at different cutting speeds, allowing for maximum process optimization.
New Multi-tasking Turning Center
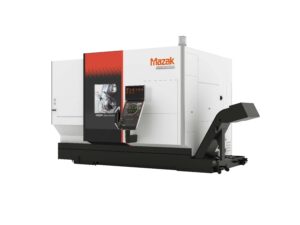
The new HQR 200/3 NEO from Mazak Corp. (Florence, KY) has two spindles, one of which is a high-torque 6,000-rpm, 14.6 hp (10.9 kW) milling spindle, and three turrets — two upper and one lower — for superior DONE IN ONE® part processing opportunities and high-volume throughput in single setups. The drum-style turrets provide 12 tool or 16 tool positions along with rotary tool capability, and the HQR 200/3 NEO’s new third turret only marginally increases the machine’s overall footprint.
The main spindle handles 4″ bar stock while the second spindle is capable of processing bar diameters up to 2.99″ (76 mm). With enhanced automation capabilities, the machine easily integrates with available bar feeders as well as with an optional workpiece loader/unloader and conveyor that handles parts 4″ in diameter x 7.09″ in length for fully 24/7 lights-out operations.
For the HQR 200/3 NEO, Mazak developed its MAZATROL SmoothG3 control to support three-turret machine functionality. The control gives users a clear specific display of the turrets for programming and operational ease of use and to ensure process security.
As part of the MAZATROL SmoothG3 control, the machine includes Mazak’s Ai Thermal Shield. The function ensures stable machining accuracy through machine-learning-enhanced heat displacement compensation.
Every Mazak machine is backed by Mazak MPower Complete Customer Care, the industry’s most comprehensive machine support program. Plus, Mazak Capital Equipment Financing allows shops to easily move their manufacturing forward with one-stop, factory-direct financing on Mazak equipment.
New Gantry Loaded, Single Spindle CNC Turning Center with Y-Axis Milling Function
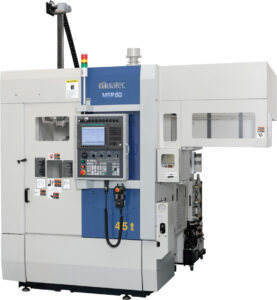
Murata Machinery USA (Muratec) (Charlotte, NC), offers the groundbreaking MSR60, a powerhouse single-spindle CNC turning center with Y-axis milling capabilities for multitasking machining. With a directly coupled 8,000 rpm live tool spindle motor, this machine is engineered to reliably deliver high-speed precision, a compact footprint, and maximum productivity through integrated built-in gantry loader automation.
The MSR60’s compact design and advanced automation capabilities allow for a space-saving layout that maximizes productivity per unit of floor space. Because it integrates milling and turning, this machine is ideal for high-mix, low-volume production environments. Like its “big sister,” MWR120, a first-of-its-kind, front-facing horizontal twin spindle turning center, the MSR60 introduces Y-axis and milling capabilities previously unavailable on a single-spindle machine.
With its automation at its core-based design, the MSR60 is a CNC turning center with front-facing 6-inch/8-inch chucks equipped with a Y-axis. It has a single 10-station turret, an X-axis stroke of 240 mm, a Y-axis stroke of ±60 mm, a Z-axis stroke of 200 mm, and a maximum spindle speed of 6,000 revolutions per minute.
The MSR60’s width is 1,555 mm, and its depth is 2,350 mm, half the size of the MWR120, but it has twice the range of motion or stroke typical for a turning machine its size. “The MSR60 enhances Muratec’s overall single-spindle lineup, combining powerful processing capabilities within a compact design tailored for job shops just starting their automation journey,” said Jeff Kalmbach, general manager, Machine Tools Division, Murata Machinery USA. “With the introduction of milling and Y-axis functionalities previously unavailable on a single spindle turning machine, the MSR60 enables extreme multitasking, creating complex shapes from raw materials to finished products without the need for changeovers. This innovation addresses the industry’s near-constant labor shortage and eliminates the necessity for secondary operations, streamlining production and boosting efficiency.”
Turn-mill Center is “Swiss Army Knife” for Machinists
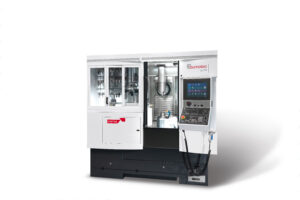
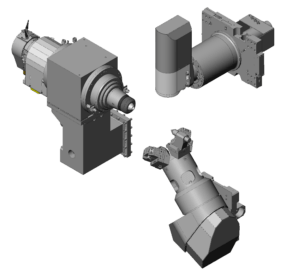
The “PRM” configuration of the Bumotec S191neo enables the production of two pieces in one cycle.
The Bumotec 191neo from Starrag (Hebron, KY) is just as versatile as its predecessor and it makes operation easier, above all thanks to the new human-machine interface. The machine combines concentrated expertise in a very ergonomic housing. With its large glass panes and optimally positioned access doors, it offers a good view of the various areas of the machine and improved access for operators. A light strip provides information about the operating status at a glance. Thanks to the ergonomic design, staff can switch between screens with a simple finger movement.
The progress of ongoing machining operations, the configuration of programming or the monitoring of production can be tracked in real time. All in all, the turn-mill center is intuitive and easy to learn to use.
A clear advantage in view of a job market in which highly qualified, skilled personnel are in short supply.
Starrag supplies the machining center in versions with vice “P”, multiple vice “PRM”, counter spindle “R”, counter spindle/vice combination “RP” and with a bar capacity of 42 mm, 50 mm or 65 mm. The Bumotec 191neo is not just one machining solution, but 12 different machines on a single platform. According to Starrag, it is only with this variety that the special requirements of typical users from medical technology, the luxury goods industry and micromechanics can be optimally fulfilled both from an economical and a technological perspective.
The Bumotec 191neo operates with great stability, reliability and productivity even without user intervention. Thanks to the reduction in tool change time by about 15%, it meets high cycle time requirements and thus reduces unproductive downtime.
The increased torque of the Starrag milling spindle and the electric motor-controlled pick-up unit, which is 12% faster than before, are strong points in favor of the newcomer. The Bumotec tool magazine with more than 90 tool places as standard has a broken tool sensor working in parallel, just in case. When used in combination with a Bumotec palletizer or a robotic automation cell, continuous production around the clock can be achieved that only needs to stop for preventative maintenance, if that.
New Horizontal Lathe Designed for Small Parts
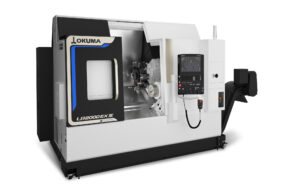
Okuma America Corp. (Charlotte, NC) has launched a new addition to the company’s horizontal lathe lineup — the Okuma LB2000 EX III. This new product joins the company’s flagship line of LB-EX series lathes. Equipped with a 140 Flat spindle, the new LB2000 EX III is designed to create finely tuned small parts or complex components when paired with optional MYW (milling, y-axis, and sub-spindle) offerings. Hallmarks of the LB-EX lathe family include high-accuracy machining partly attributed to the machine’s rigid construction. Additionally, the LB2000 EX III is equipped with a high-power, high-torque PREX motor built to deliver powerful, high-quality machining for heavy and high-speed cutting. This, in combination with Okuma’s Thermal-Friendly Concept, which minimizes thermal growth during the machining process, ensures machining accuracy and thermal stability.
The new machine is also equipped with Okuma’s new OSP-P500 control, a next-generation open-architecture control designed exclusively for Okuma machines. This next-generation control enables numerous market-leading intelligent machining technologies, including:
- Windows®-based, open-architecture platform for easy integration to applications on the Okuma App Store and beyond.
- Greater processing power with dual-core computer processors.
- Embedded, robust cyber-security features to protect operations and data.
- On-board energy management and green machining capabilities with Okuma’s proprietary Thermo-Friendly Concept & ECO suite plus functionality.
- Full-color touchscreen in two sizes: 15” screen or 21.5” screen, based on machine model.
- Combination of user-friendly hard and soft keys; QWERTY keyboard.
- Space-saving, modern design with ergonomic tilt and swivel capabilities; pulse handle options also available.
Innovative Broaching Solutions for Both CNC Lathes and Machining Centers
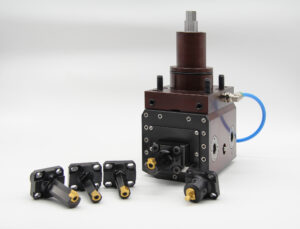
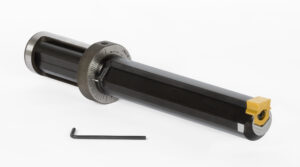
Platinum Tooling Technologies Inc. (Prospect Heights, IL) now carries REV broaching tools in North America. REV is a manufacturer of innovative broaching solutions for CNC lathes and machining centers. The tools are ideal for machining simple keyways or internal and external profiles, both teeth and splines. Common profiles including square and hexagon are easily achieved and custom profiles are available. REV Broaching Tools offer excellent performance with long insert life and high surface quality.
The REV motorized broaching tool is designed for use on live tool lathes. Single machine set-up eliminates the need for secondary operation or outsourcing. REV tools are ideal for high production runs, offer easy installation and fast processing time. These tools are designed for maximum rigidity, offer long tool life and an excellent finish.
REV static broaching tools are for use on CNC lathes with or without Y-axis. They offer a patented eccentric bushing which eliminates alignment errors for machines without a Y-axis. The tools have a sturdy two-piece construction and are ideal for smaller runs. They are designed for use in boring bar holders on lathes and for use in collet chucks or Weldon holders on machining centers. REV tools allow for a wide variety of standard and custom profiles and sizes.