Trailblazing Accessories Ensure Quicker Production Cycles and Increased Output
Machine tool accessories reduce downtime and speed up your machining operations.
Posted: November 16, 2024
Whether it’s through quick-change receivers, automated tool holding systems, high-precision guide bushings, or modular workholding solutions, these advancements help metalworkers improve productivity.
Automation-Ready Tool Holding System

The new PGA (automatic) 9500 from REGO-FIX USA (Whitestown, IN) is automation-ready and provides a simple way to automate the tool setup process when using the popular REGO-FIX powRgrip tool holding system. As such, it allows tools to be set up unmanned and around-the-clock.
For seamless integration, the PGA 9500 easily connects via a robot to other equipment as well as to tool storage areas. Its automatic door and easily controllable clamping device make the PGA 9500 well suited for working within existing automation systems. Its space-saving design, safe operation and the fact that it generates no heat or hazardous fumes make the clamping unit the ideal solution even in limited spaces.
REGO-FIX developed its powRgrip system for stable tool holding when machining parts made from all types of materials. The system’s press-fit tool holding delivers higher precision, with greater vibration damping for longer tool life and superior part surface finishes.
PG system tool clamping/unclamping units use automated tool setters that load a tool into a holder in under 10 seconds, ready for immediate use. The units achieve a 1,100 Nm clamping torque rating, the industry’s highest, and their 0.0001″ TIR is guaranteed throughout five years or 20,000 tool setting cycles.
New Workholding Products for Large Parts and Increased Flexibility
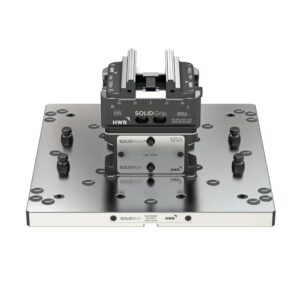
HWR Workholding USA (Noblesville, IN) offers multiple new additions to its SOLIDLine family of innovative zero-point workholding. The new products include SOLIDGrip MAXX for large workpieces, SOLIDBolt FLEXX for direct integration with pallets and tables of select machine tool builders, pyramids for increased capacity in 5-axis machines, and mounting plates to streamline tombstone setups.
With a maximum clamping range of 800 mm (31.5”), SOLIDGrip MAXX offers extremely secure holding of large parts. The product capitalizes on SOLIDGrip’s modular design, allowing two standard vises to be quickly converted to one large-capacity vise and back again in minutes. For parts that are large in both width and depth, two SOLIDGrip MAXX vises can be applied as a pair. Vise jaws are available in smooth, serrated and heavy-duty toothed versions to ensure an optimal match to every application.
Developed to simplify and streamline operations, SOLIDBolt FLEXX allows workholding components to be quickly and easily installed. The system enables pull studs to be secured directly to the existing hole pattern on a machine’s table or pallets. Following this, the integrated zero-point plate on SOLIDGrip products allows for fast installation of a wide range of workholding products, including vises, risers, chucks, pyramids and more.
SOLIDBolt FLEXX is currently available as a standard product for select machine tools from DMG Mori, Makino, Matsuura, Mazak and Yasda. HWR will be expanding the product to machines from other builders, and also offers customers custom versions tailored to their specific machine make and model.
For 5-axis machining applications, HWR has launched a series of pyramids that can hold up to three workpieces at a time. Standard products can mount either 46 mm (1.8”) or 77 mm (3.0”) vises, accommodating a maximum vise length of up to 120 mm (4.7”). The pyramids can be directly mounted to a machine’s table or pallets, and they significantly reduce non-cutting time caused by loading and unloading workpieces from the work area.
Expanded Line of Quick Action Sliding Locks Includes a Heavy-duty Version
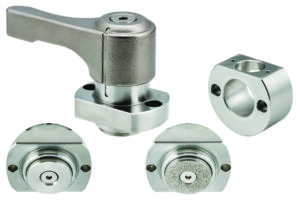
Fixtureworks (Fraser, MI) has expanded its line of quick action, quick release workholding locks for sliding adjustment to include a new heavy-duty variety — the QCPSS Heavy Duty Sliding Locks. These push lock clamps improve set up time and reliability in fixturing applications. They provide easy locking with a 90° turn of the handle for slide and angle adjustment without the need for tools and are versatile enough to clamp on various objects such as square bars, round shafts and linear rails. These heavy-duty clamps provide quick and easy locking with a high clamping force. An internal spring keeps the clamping force constant to prevent over/under tightening. An indication line and the “touch” of a click allow users more secure and reliable operation.
Two tip types of the QCPSS are available: A flat tip that helps minimize damage to an object, and a diamond-surface tip that provides high holding force. Both versions provide 247 lb. clamping force. The clamp body is made from 303 stainless steel. The handle is made from 304 stainless steel. The sliding locks are supplied with two M4 socket head screws for mounting.
For clamping onto a round shaft, a shaft collar is also available. The shaft collar accessory, available in diameters from 44-60 mm, is used to hold round shafts with a diameter of 20 mm or 25 mm.
The shaft locking clamps are designed to positively lock a shaft quickly. As the handle is turned, the piston is pushed out and locked with balls, allowing the gripper tip to clamp firmly onto a bar or shaft. When the handle is turned back, a spring releases the locking block allowing the shaft to move freely. The adjustable push lock clamps are ideal for sliding lock applications that require frequent disassembly and/or changeover and help improve setup time and reliability.
Quick-change Receiver Shows 90% Reduced Change Over Times
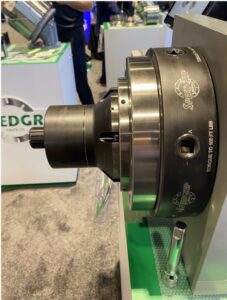
Speedgrip Chuck Co.’s (Elkhart, IN) QCR Quick- Change Receiver is a manually actuated cam-lock receiving plate that attaches to CNC lathe spindles and dramatically reduces the time needed to change workholding clamping devices.
Similar to tool retention in the spindle, the QCR features automatic release of draw connections. With the QCR Quick-Change Receiver, the time needed for operators to effortlessly switch ID/OD collets, jaw chucks or face driver workholding devices on their machines is cut from an hour to five minutes, making them well suited for just-in-time production.
The QCR Quick-Change Receiver is available for all standard nose configurations, for spindle sizes that run from A2-5 through A11 and flatback spindles. For added versatility, the easy-to-use QCR Quick-Change Receiver also comes in a through-hole design for through-spindle bar feeding operations.
“By engineering the receiver so that only two adapter plates are necessary, we’ve made the QCR Quick-Change Receiver as modular and standardized for our customers as possible,” said Speedgrip Chuck Co.’s President Matthew Mayer.
Certification for 52/96 Workholding System is a Testament to High-quality Products
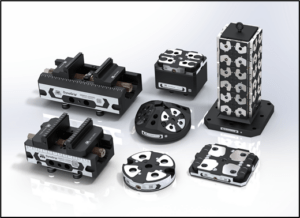
Mate Precision Technologies (Anoka, MN), a leading provider of innovative workholding solutions, announces its certification as a DMG MORI DMQP partner for its 52/96 workholding system. This certification, a result of its unwavering dedication to quality and reliability, is a testament to Mate’s commitment to providing high-quality and reliable products to its customers.
DMG MORI is a global leader in the manufacturing of machine tools and has established the DMQP (DMG MORI Qualified Products) program to recognize partners that meet their strict quality standards. The certification process thoroughly evaluates the partner’s products, processes and services. Mate Precision Technologies has successfully met all the requirements and has been recognized as a trusted partner by DMG MORI.
Mate’s workholding system, renowned for its versatility and efficiency in holding a wide range of workpieces in machining operations, offers unparalleled accuracy and repeatability, making it the go-to choice for precision machining. With the prestigious DMG MORI DMQP certification, customers can rest assured that the Mate’s workholding system meets the highest standards of quality and reliability set by DMG MORI.
This certification is a significant milestone for Mate Precision Technologies, reinforcing its position as an industry leader in metalworking. With the DMG MORI DMQP certification, customers can trust the quality and reliability of Mate’s workholding system. The company’s commitment to innovation continues to drive the development of cutting-edge solutions, empowering manufacturers to enhance their productivity and efficiency.
Guide Bushings for Swiss Type CNC Lathes
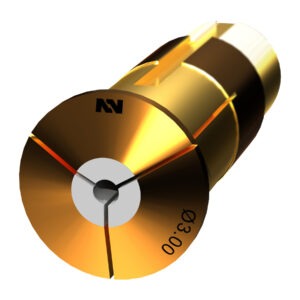
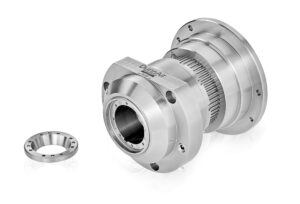
Platinum Tooling Technologies, Inc., (Prospect Heights, IL) now offers products from Dunner, a manufacturer of guide bushings for Swiss Type CNC Lathes. Producing guide bushings since 1935, Dunner has the know-how to manufacture guide bushings in different bore profiles, guide lengths and insert material. In addition, silicone sealants can be applied to limit chip penetration. All guide bushings are available in standard (15 microns or less), ultra-precision (5 microns or less) and ultimate ultra-precision (2 microns or less).
The company manufacturers bronze, ceramic and titane (Meehanite®) guide bushings for customer machining needs. All guide bushings are ready for machine use with finished internal surfaces and geometries designed to offer the best result with nominal size material.
Manufactured from a special cast iron, titane/Meehanite offers an excellent compromise between the coefficient of friction and wear. Suitable for stainless steel, titanium and other materials with a tendency to “load up,” it minimizes part marking and is used extensively in medical parts production.
Using high-tech ceramic, Ceramic/NewSurf® offers one of the lowest friction coefficients on the market. Specifically designed for titanium, stainless steel and other difficult materials, it’s suitable for the tightest production tolerances. Ideal for medical implants, it’s only available in round profile.
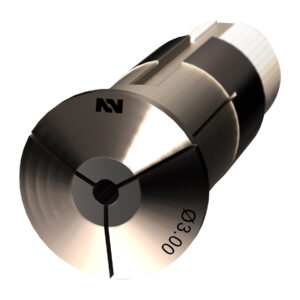
Designed with steel body and bronze insert for durability, the bronze guide bushing is the most cost-effective material to prevent marking. Best suited for non-medical parts production, the guide bushing is suitable for all non-copper materials and clamping workpiece material up to h8 tolerance.
Dunner’s DunnAir Adaptive Guide Bushing System is designed to replace the original guide bushing supplied by the machine builder. The easy-to-use system adds flexibility and consistency to the machining process. With this system, the need for ground stock is eliminated. DunnAir is self-adjusting and consistent and offers four different positions for flexibility and control. In addition, the bushing has a clamping range of 0.5 mm (0.020”) to accommodate material variance, as well as eliminate downtime. Lastly, DunnAir is CNC controlled, so customers can choose the position based on application.