Small Shop, Big Gains
How pre-engineered weld cells can benefit business of all sizes.
Posted: November 15, 2024
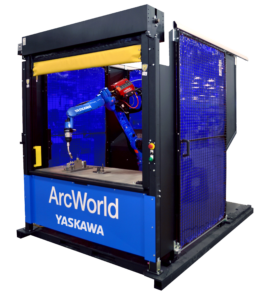
As a critical tool to increasing efficiency, safety, productivity and profitability in demanding manufacturing environments, robotic automation continues to permeate the industrial landscape. To stay competitive, decision makers are implementing a variety of advanced solutions, including cost-effective turnkey work cells for the fabrication of small- to medium-sized parts.
Appealing Turnkey Offerings for Optimal ROI
Expected to exceed a compound annual growth rate (CAGR) of 14% by 20341, the robotic work cell market is anticipated to continue rapid growth – with systems impacting a range of processes for assembly, welding, painting, handling, inspection and more. That said, when leveraged correctly, these highly productive systems offer attractive features and inherit incentives, facilitating better payback and return on investment (ROI), such as:
Pre-engineered to Save Time and Money
A primary advantage to opting for a turnkey welding work cell is that expert design and extensive engineering has already taken place – with the system being further enhanced over many iterations for intentional continuous improvements. Subsequently, this pre-engineered product improves on many factors ranging from installation time, system speed and part quality to reduced costs. Likewise, valuable resources are not spent on designing a solution from scratch in the first place and can spend time on application specific modifications.
Production-ready, straight-out-of-the-box solutions that come on a common base with integrated cable management are highly portable and can be deployed quickly on-demand with ease, facilitating greater uptime. Depending on the application and integrator, basic robot jobs may be included on the teach pendant to accelerate start-up time, including the opportunity to provide offline programming from a computer model before a physical system is complete.
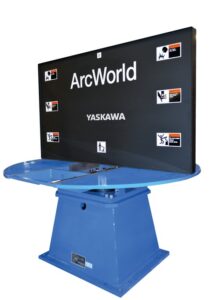
Designed to be Safe in Every Aspect
Important to any operation, worker safety is the top priority during turnkey system design. Safety standards and regulations are well defined by ANSI/RIA R15.06, but applications can require additional safety precautions. Pre-engineered cells account for these latest safety standards and features, maintaining compliance with industry regulations and ensuring the well-being of robot programmers, work cell champions and other associated personnel. Depending on the type of system, safeguarding will vary. Along with a built-in Functional Safety Unit (FSU) to ensure robot operation occurs in areas clear from operator presence, standard weld systems will typically have safety fencing, welding curtains, interlocking access doors and required human interference devices, like an emergency stop (e-stop) button.
Collaborative work cell safeguarding can look a lot different, sometimes requiring no fencing at all. However, complete solutions built for the risks of the application, such as the ArcWorld HC, provide a total safety environment with: Power and Force Limiting (PFL) technology, provisions for fume mitigation, arc flash protection and an e-stop. Ergonomically designed pendants and roll-up-doors, when needed, also contribute to enhanced worker safety.
Enables Little-to-no Trial and Error
A proven, pre-engineered purchase allows manufacturers to bypass the trial-and-error phase that comes with custom integration for a lean manufacturing fit. Custom turnkey systems are thoroughly tested throughout the build process, which takes time and allows most testing and debugging taking place before shipping occurs.
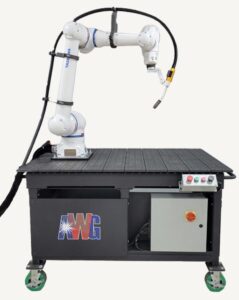
Facilitates Easier Upgrades and Retrofits
As market demands evolve, system upgrades may be needed to increase capacity, enhance quality, accommodate specifications or other tasks. From adding ready-to-use standard options such as light beacons or human machine interfaces (HMIs) to changing welding power supplies, torch types/brands or positioners, there are multiple items manufacturers could upgrade to optimize operations.
Thanks to generational revisions and spare parts availability, standardized systems are usually easier to upgrade than custom integrated solutions. Incremental design improvements to work cells result in more user-friendly systems that can be easily modified, helping to minimize downtime when maintenance or enhancements are necessary. Likewise, turnkey systems with standard components enable smoother part delivery for more expedient upgrades. Fabricators thinking about a simple system upgrade may want to consider the addition of:
- Dress packs – ideal for securing, protecting and managing robot cables and hoses, dress packs can minimize interference, reduce wear and tear, and reduce downtime.
- Weld torches – as mentioned, upgrading a weld torch can make a vast improvement in access and sometimes consumable use. Specialty torches, like servo “pull” torches, also work in tandem with specialized power supply waveforms to increase travel speed and deposition rates and decrease heat input while reducing scrap and rework.
- Servo positioners – providing the versatility and accuracy many job shops require to meet stringent demands, these positioners help to timely execute a range of welding tasks by accessing all welds without manual intervention, as well as providing simultaneous processing of parts while loading/unloading the opposite side.
- Other options – from increasing safety to gaining better weld access, there are multiple options fabricators could implement. To enhance welding safety, air filtration may be in order. To accommodate various part sizes and gain better weld access, the use of coordinated motion may be helpful. The first robot company to develop this function, Yaskawa robots can easily maneuver in the same space as spot guns, external positioners and more. Robust multi-tasking software facilitates easy programming of coordinated motion, minimizing system downtime in the process.
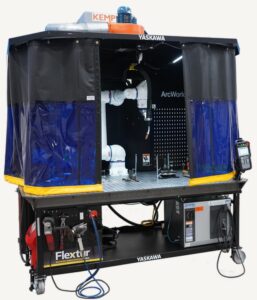
Unique application requirements will typically require a variation of a standard work cell. Innovative solutions such as this often contain multiple robots to minimize weld and cycle time, while maximizing output. High-speed positioner options and leading-edge process technology can also be included to fulfill stringent productivity demands.
Offers the Best Cycle Time
Due to their pre-engineered nature, turnkey work cells are optimized for performance, ensuring that manufacturers can achieve the best cycle time possible without sacrificing reliability. Over time, the use of these systems can lead to increased productivity for greater profitability.
Key Metrics for Moving Forward
From machine tending to arc welding, there are dozens of pre-engineered systems available to augment production processes. Along with this, various options exist to accommodate budgetary needs. Whether acquired through a robot supplier, automation integrator or a Robot as a Service (RaaS) provider, fabricators looking to integrate turnkey systems for the first time should consider concepts such as cost, integration, training and ROI.
Perhaps the most significant factor first-time work cell adopters should weigh is finding the most cost-effective option. Frequently offering quick payback, pre-engineered solutions offer the best value for quickly and reliably modernizing workspace, maximizing efficiency and improving quality. Systems that integrate smoothly into current workflow with little disruption are ideal, along with user-friendly options that leverage ease-of-use tools for easier programming and a shorter learning curve.
Collectively, these things work together to help calculate a system’s perceived value and ROI. Manufacturers that have a keen understanding for their reasons behind automation, along with these concepts, should be able to determine the most effective solution to drive welding success.
End Note: 1. Robot Cell Market Size to Surpass US $12.8 Billion by 2034, GlobeNewswire, 2024