Extending Cutting Tool Life
Minimize tool replacement expenses, while maintaining consistent and quality output.
Posted: November 16, 2024
Longer tool life, higher precision, and increased productivity means lower operational costs and better overall performance in demanding machining applications.
ProACT-Mill Series Provides Economic and Ecological Advantages
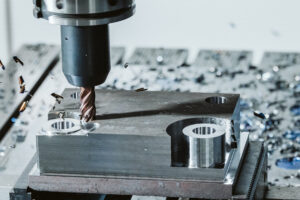
CERATIZIT (Schaumburg, IL) introduced the ProACT-Mill universal solid carbide milling cutter series at the recent IMTS 2024. The milling cutters bring together the latest geometry and coating technologies. In addition, the series is manufactured from CERATIZIT’s upGRADE line of recycled carbide.
In testing, ProACT-Mill milling cutters delivered up to 30% higher performance compared to other universal tools. Its newly developed coating also contributed to longer tool life.
To guarantee unbeatable cutting edge stability, the milling cutter features a radial clearance face. The face-finishing chamfer ensures superior surface quality with base machining, while cutting edges with an irregular pitch specifically suppress vibrations. Ramp milling and helical milling are possible up to a 30°angle, and thanks to the acoustics of the ProACT-Mill UNI, even with high infeed values and full-face milling, cutting noise is limited.
The ProACT-Mill UNI with a cutting edge length of 3xDC is particularly suitable for series production and trochoidal machining. Innovative chip breakers in a radial design deliver the longest possible tool life and break chips to lengths of 1xD, which are then evenly and consistently removed via special flute shapes. Thanks to the minimal conical tool core, the 5-flute cutter runs quietly even with a high lateral width of cut. The tool’s HB shank provides force transmission, while its reinforced core ensures even force distribution throughout the milling process.
For maximum material removal rates, the geometries of the ProACT-Mill UNImax — applicable for depths of cut of up to 2xDC — is the ideal solution. The tool is available with HA and HB shanks for unbeatable force transmission and balance qualities. With the variable tool core, optimum force distribution was the key focus in its development.
The ProACT-Mill series is made from CERATIZIT’s upGRADE, CT-GS20Y grade of recycled carbide. Customers gain both economic and ecological advantages thanks to a low product carbon footprint (PCF). upGRADE has the highest material circularity in its category because 50%-to-99% of the powder is reprocessed using advanced metallurgical technologies and 100% renewable energy. CERATIZIT also featured an upGRADE raw material rod at IMTS as a complement to the new mill series.
“What’s special about upGRADE is the significantly smaller carbon footprint generated during production, compared to carbides from conventional production,” explained Michael Wucher, global technical product manager at CERATIZIT. “We achieve this by using 99% secondary raw materials in the form of recycled carbide cutting tools.”
www.cuttingtools.ceratizit.com
A Truly Versatile Shoulder and Face Milling Concept
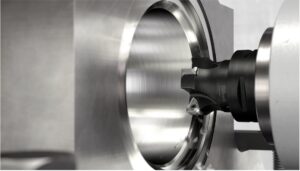
Sandvik Coromant (Mebane, NC) CoroMill® MS60 is tailored for 90° shoulder milling operations in steel and cast iron, but versatile enough to extend its competence across areas such as face milling and various ramping applications.
“CoroMill MS60 is a universal shoulder and face milling solution, primarily designed for roughing to semi-finishing operations in steel and cast iron, with two geometries capable of handling both these application areas as well as secondary areas ISO M and ISO S,” said Jocelyn Lanaro, global product application specialist at Sandvik Coromant. “As such, it is possible to handle mixed material batches, including stainless steel and nickel-based alloys, without changing inserts.”
As a robust multi-edge concept with positive cutting action, cutting forces are low for vibration-free machining, which translates into a high cost-efficiency per edge. Featuring a true 90° entering angle, CoroMill MS60 is mainly a shoulder milling tool — even though it excels in many other areas as well.
“From general milling operations to side milling, slot milling, helical ramping and face milling — CoroMill MS60 truly is an all-round solution,” Lanaro said. “It is usually the first tool chosen during the early stages of universal milling operations, handling the roughing to semi-finishing stages, leaving the finishing to dedicated solutions.”
Another standout feature to highlight is the direct pressed, six-edged inserts: “They are manufactured using a highly advanced multi-axis pressing technology, meaning it has been possible to gather both a smooth cut and ramping capability in the same insert, enhancing the versatility of the product,” Lanaro said. Providing four different diameters in both metrics (50 mm-to-100 mm) and inches (2”-to-4”), CoroMill MS60 offers a compact yet comprehensive range, making both selection and usage easier.
Custom PCD Tooling for High-Precision, High-Volume Machining of Aluminum
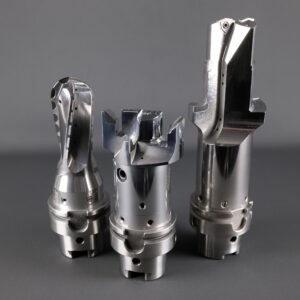
Custom designed polycrystalline diamond (PCD) tools from UC Tools, partners with Monaghan Tooling Group (Dayton, OH), feature complex geometries to allow the intricate machining of aluminum components. Developed by the global leader in manufacturing bespoke PCD tipped round tools, they can combine multiple machining applications like boring, reaming, drilling, and milling, within a single tool, thus saving time and driving down the cost per piece. High wear resistance inherent with PCD tipped tools extends tool life and delivers a lower cost per machined component. Solid carbide bodies can be fitted with a variety of shanks, including HSK, CAT, BT, and Flange Mount (module), to suit any high-volume application. UC Tools custom designed PCD tools are ideal for high-volume precision machining application on aluminum castings such as ABS & ESP brake valve bodies and master cylinders, rack and pinion housings and electric steering housings, transmission valve bodies and cases, cylinder heads and cylinder blocks, diesel throttle bodies, fuel pumps, turbochargers, water pumps, and small engine and drivetrain components for lawn and garden, recreational vehicles and more.
In addition to developing custom PCD tooling, UC Tools re-tips and re-grinds any PCD tools to extend their service life and maximize performance of the initial tooling investment. With vast experience, unparalleled manufacturing capabilities, and state-of-the-art CAD, CAM, grinding, EDM and inspection equipment, UC Tools delivers high-quality products with industry leading lead times.
In addition to PCD tooling, Cermet and carbide tipped tooling is also available to suit application specific requirements. Polycrystalline Cubic Boron Nitride (PCBN) inserts, milling cutters, and indexable inserts upon request.
New Solid Carbide Milling Cutters
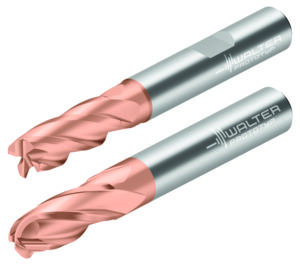
Walter USA’s (Greer, SC) ME232 and ME432 Perform solid carbide milling cutters add to its range of solid milling cutters. The tools can be used universally for diverse milling operations with various workpieces, meaning one tool is appropriate for a large range of material types. The Perform cutters are designed to be highly economical and are made with the WJ30ED universal milling grade.
The ME232 Perform has a cutting diameter (Dc) from 1/8″ to ¾”, and from 2 mm-to-20 mm, and is available with two, three, four, five or six effective flutes (z2, z3, z4, z5 or z6). The z2 and z3 tools are primarily for slot milling and profile milling, the z4 is for ramping, slot milling and helical milling, the z5 is for roughing and finishing, and z6 is for dynamic milling and finishing. These series offer cutting-edge length (Lc) from 1 × Dc to 3 × Dc.
The ME232 is suitable for milling steel, stainless steel, cast iron, nonferrous metals and heat-resistant super alloys (ISO P, M, K, N and S material groups). The tools can be used in a range of industries, including mechanical engineering, automotive, energy and tool, mold and die making. The ME232 Perform features the newly developed high-performance cutting (HPC) geometry, with helix pitches tailored to the number of teeth. For example, the z4 cutter has a variable helix geometry with 35° and 38° helix angles.
In the application testing or milling 4140 steel and stainless steel, the ME232 cutter increased the tool life distance 244% and 340%, respectively, versus the competitor.
The ME432 Perform is a ball-nose endmill for roughing and finishing freeform surfaces. The cutting diameter range is from 1/16″ to 5/8″, and from 1 mm-to-20 mm. It is available with two or four effective cutter teeth (z2 or z4) and has a 30° helix angle.
The Walter lineup of products consists of three categories of tools. Supreme tools indicate the highest level of technology and performance available. Advance tools indicate products efficiently balanced between price and performance, and Perform tools are products that provide an economical solution with focused importance on price ideal for small batch production.