Boost Welding Operators Output By Teaming with a Collaborative Workforce
Cutting-edge real time visioning systems and advancements in cobot welding ensure precision, reproducibility, and controlled and reliable production.
Posted: November 16, 2024
Welding automation firsts and user-friendly programming make collaborating with welding robots and cobots more accessible and efficient, successfully carrying out processes that traditionally required highly skilled operators. The advances allow operators to focus on higher-value or other tasks while the automation conducts repetitive welds, as an example.
Cobot Welder now Supports Miller’s Auto DeltaWeld
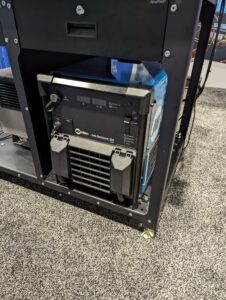
Hirebotics (Nashville, TN), a leading provider of collaborative robots for metal fabrication, launches support for the new Miller® Auto DeltaWeld™ with its Cobot Welder. The Miller Auto DeltaWeld System is a MIG/flux-cored, pulsed-capable power source designed for cobots. With this new addition to Hirebotics Cobot Welder, the user experience becomes even more streamlined.
Beacon, a Hirebotics smartphone app, now controls the entire cobot welding setup. Unlike other cobot solutions, Hirebotics Beacon-powered Cobot Welder lets the user control everything in one place — a simple smartphone/tablet interface. This makes the process easier and faster compared to systems where welders must go back and forth between the teach pendant and the power source.
Beacon is cloud-based, allowing total remote and local cobot control. In Beacon, users can adjust settings such as:
- Switching processes between CV and pulsed MIG
- Wire feed speed (WFS)
- Arc length
- Crater fill time
- Weave action
- Pre and post flow time
- Burnback, retract, and hot start settings
The new Miller Auto DeltaWeld integration into Hirebotics Cobot Welder future-proofs the system. With remote software updating, future welding features and functions can be easily integrated with the Cobot Welder. “While the Auto DeltaWeld Basic is designed for simplicity, we at Miller still want to provide top of the line waveforms,” said Sam Nolan, product manager at ITW Miller Welding Automation. “As we update and expand our welder functionality, Hirebotics ability to provide online updates is a powerful tool to ensure their customers experience the latest in welding technology.”
The Miller Auto DeltaWeld provides exceptional reliability and welding quality on carbon steel, stainless steel and aluminum. It’s designed for sheet metal, structural steel, and heavy industrial manufacturing.
“Cobots are designed to provide simple, safe automation,” Nolan said. “The Auto DeltaWeld Basic was built just for that. We strive to provide Hirebotics with the ability to provide the best software/hardware experience to keep the cobots easy to use and operate.”
Hirebotics Cobot Welder is a straightforward, app-controlled, turnkey, off-the-shelf welding automation solution. Beacon automatically recommends welding parameters using artificial intelligence (AI), saving time and improving the weld quality. Users can use recommended and previously saved settings, or input welding parameters manually.
Hirebotics Cobot Welder requires no programming or robotics skills. Beacon only requires the settings welding professionals are used to, like WFS and voltage.
Small- and Medium-sized Enterprises can Achieve Perfect Weld Seams 24/7
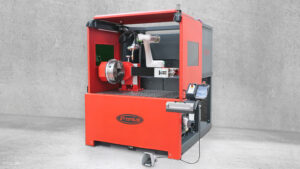
Although automated welding processes achieve significantly more consistent welding results, small and medium-sized businesses frequently still struggle with automation. High acquisition costs for welding robots and professional programming expertise are at odds with small batch sizes. The CWC-S Cobot welding cell from Fronius (Portage, IN) provides a solution to this mismatch.
Thanks to precise torch movements with a repeatability of +/- 0.04 millimeters, weld reproducibility is guaranteed in the cobot welding cell every time — even in series if necessary. Intelligent Fronius welding technology controls the welding process and records all welding data as required. The WeldCube data management software — optionally available with the welding cell — serves to store and evaluate these data.
“Programming a CWC-S is intuitive and can be quickly learned by any welding specialist; programming know-how is not required,” explained Christian Neuhofer, product manager at Fronius Welding Automation. “Components can even be loaded and welding programs started by trainees. This saves on personnel costs and frees up professional welders for more challenging work — making their job more attractive.” This is an advantage that should not be underestimated when searching for skilled workers to add to the team.
The welding torch is manually guided to the starting points, position points, and end points on the component and these are confirmed by pressing a button. The software uses this information to calculate the welding contours and welding sequence, while the required welding parameters can also be selected quickly using predefined characteristics. Motion commands such as “pendulum parameters” or “weld job” can be inserted by means of dragging and dropping on the touchscreen of the cobot control.
Before starting the welding process, the operator can simulate the welding sequence once again to detect and correct possible interference contours. Once the CWC-S is fully programmed, it welds component after component with consistent quality and at a regular speed.
The welding cell’s standard equipment includes a FANUC Cobot CX10 iA with a reach of 1,249 millimeters and a payload of 10 kilograms, and a welding table with a working area of 1,500-x-1,000-x-700 millimeters. Operator safety is ensured by a pneumatic glare shield, sliding side doors with viewing windows, and an extraction hood.
Users can choose between the tried-and-tested Fronius Welding Packages Standard, Pulse, LSC (Low Spatter Control), PMC (Pulse Multi Control), and CMT (Cold Metal Transfer) depending on the intended area of use, while the TPS 320i or TPS 400i welding systems are available for the cobot, subject to the package selected.
The standard equipment can of course be supplemented with special starter packages or the user-friendly WeldConnect app, for example. Further options include an extraction system, a rotary unit including tailstock, or the option of crane loading.
Simplify Tasks and Reduce Equipment Needs with a Lightweight Multiprocess Welder
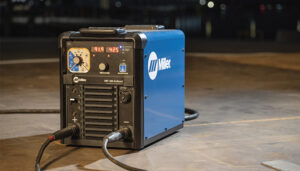
Miller Electric Mfg. LLC (Appleton, WI), a leading global manufacturer of Miller® brand welding products, announces the launch of its Miller XMT® 400 ArcReach® multiprocess welder. As the lightest and smallest machine in its amperage class, the XMT 400 ArcReach helps fleet managers and operators tackle more jobs efficiently with just one welder.
“We took a beloved tried-and-true machine and enhanced it with new features and technologies that help operators work harder and smarter,” said Dave Lambert, group president, ITW Welding. “The new XMT 400 ArcReach offers more jobsite flexibility, takes up less space and is easier to move — setting the stage for operators to amplify their productivity and push their performance to a new level.”
A hallmark feature of the XMT 400 ArcReach is ArcReach technology. It provides remote control of the power source without a control cord, saving operators time and money from having to walk back and forth to the welder, keeping the welding operator welding at the weld joint. Additionally, dedicated weld processes like gas-shielded flux-cored, TIG, self-shielded flux-cored, stick and gouge allow operators to dial in whatever they need, no matter the job.
The XMT 400 ArcReach further amplifies welding efficiency with these cutting-edge capabilities:
- Auto-Line™ technology: Allows the welder to be plugged in to any primary voltage power from 208V to 575V single- or three-phase and engine-driven generators.
- Higher duty cycle: A rating of 400 amps at 60% duty cycle achieves bigger and longer welds with a larger diameter wire and rods.
- Cable length compensation: Provides consistent weld quality by automatically compensating for voltage drop over long weld cables.
- Gouging capability: Gives operators the ability to gouge with a dedicated gouge that allows them to upsize a carbon diameter, rated for 5/16-inch.
- User-friendly interface: High-visibility and simplistic, adaptable arc controls allow operators at any skill level to find just the right settings.
- Front panel lockout: Disables the power source interface when connected to an ArcReach accessory to avoid inadvertent changes to the power source.
Fabricators can use New Welding Cobot with Their Existing Welder
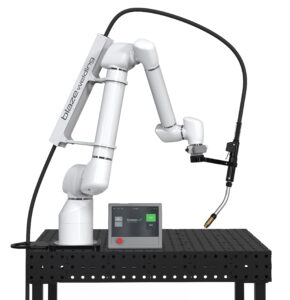
Demand for robotic welding is expanding as fabricators seek to achieve consistent, high-quality welds and faster throughput. Productive Robotics’ (Carpinteria, CA) new Blaze Welding Cobot can be used with a customer’s existing table, fixtures and welder at half the cost of other systems on the market. Unlike 6-axis robots, the 7-axis Blaze Welding Cobot can maneuver around all sides of large or complex parts and fixtures, allowing it to perform more weldments in a single setup. Blaze is engineered with Productive Robotics’ proprietary teach-by-touch and equipped to accommodate high- or low-mix volumes, short or long part runs or jobs that require quick changeovers.
“We developed and built Blaze from the ground up using our augmented intelligent OB7 Stretch model because most job shops and contract manufacturers already have welders and welding tables,” said Zac Bogart, president of Productive Robotics. “With Blaze, they don’t have to buy a whole system again. To date we’ve developed Blaze packages that are compatible with welders from eight major brands including Lincoln and Miller.”
Blaze has a 1,550 mm/61-in. radius operating sphere and requires no new fixturing. The Blaze tablet controller can hold an unlimited library of weld recipes, giving the operator command of all welding parameters including material type, voltage, wire feed, weld speed and gas flow.
A new employee or experienced welder simply uses the cobot’s control handle to physically teach Blaze to weld without programming. The cobot works safely next to its human co-workers. Live online support is provided by experienced welding and robotic experts.
For manufactures that need a complete welding system, Productive Robotics introduced its all-in-one Blaze Duo and Blaze LF automated welders at IMTS in 2022. The two-station and single-station welding systems are also run by the augmented intelligent teach-by-touch OB7 Stretch cobot. The Blaze LF has an 8’ long table designed for extra-large parts and setups. Productive Robotics designs and produces its line of collaborative cobots in the U.S.
Industry First: AI, Machine Learning Computer Vision for Arc Welding of Pipe
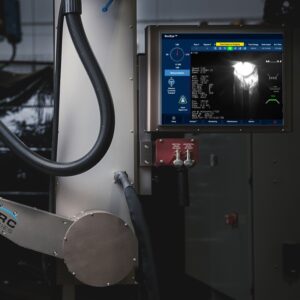
Novarc Technologies Inc. (North Vancouver, BC, Canada) a full-stack robotics company specializing in the design and manufacturing of cobots and computer vision AI for automated welding applications, has launched NovEye Autonomy (Gen 2), a real-time vision processing system that constantly improves weld quality based on data collection and model enhancement to fully automate the pipe welding process while maximizing productivity and delivering the highest quality welds.
“NovEye Autonomy (Gen 2) is an industry-first as we have developed the intelligence to fully-automate the welding process,” said Soroush Karimzadeh, CEO of Novarc. “This is an accomplishment that has resulted from years of data collected through machine learning, and we are extremely excited to be able to offer this solution to the industry.”
NovEye Autonomy (Gen 2) is the only AI machine learning real-time vision processing system that constantly improves welds based on data collection and model enhancement. NovEye Autonomy gets smarter as it continuously improves through a terabyte-scale library of welding videos, ensuring unmatched precision and reliability.
The software is embedded in the control system of the cobot and controls the weld pool in exactly the same way a human welder would, allowing the boring, repetitive welds to be delegated to the robot. The autonomous welding process enables uninterrupted welding due to NovEye Autonomy (Gen 2’s) multi-pass and multi-layer autonomous welding system, which is able to handle real-world pipe fitting inconsistencies like HiLo and varying root gaps. NovEye Autonomy (Gen 2) can immediately detect and adapt welding parameters to maintain weld integrity.
“NovEye Autonomy (Gen 2) is a truly adaptive welding solution with real-time vision processing and an advanced, complex sensory system,” Karimzadeh said. “It’s powered with advanced, real-time control due to its sophisticated AI, and powerful hardware.”
Fabricators and contract manufacturers worldwide are held to strict standards to provide sophisticated welds for industries such as aerospace, food and beverage, mining, energy, pharmaceutical, shipbuilding, chemical processing, and water treatment and desalination. All of these industries stand to benefit from NovEye Autonomy (Gen 2), which enables high quality welds with zero operator intervention, maximizing productivity and minimizing errors.
As well, NovEye Autonomy (Gen 2) can easily integrate into existing manufacturing processes of customers across a range of industries. The Spool Welding Robot — the hardware component of NovEye Autonomy — is designed with a very small footprint, but a very long reach, enabling it to fit in almost all fabrication shops, and easing the adoption of automation.
Automation is a very big milestone for the welding industry, dramatically reducing human exposure to all welding hazards as it positions the operator several meters away from the welding arc and noxious welding fumes. With NovEye Autonomy (Gen 2), operators can program the weld, and observe the weld away from the arc, reducing the risk of exposure to dangerous fumes and radiant heat. Also, muscle fatigue is reduced as the welding process is fully automated: ultimately, a win-win for the welder and the pipe shop, delivering X-ray quality welds, every time, with zero operator intervention.
High-efficiency, High-consistency Cobot Programming
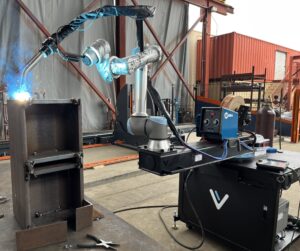
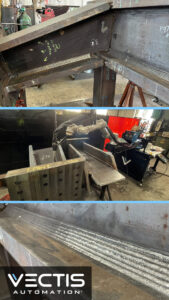
Vectis Automation’s (Loveland, CO) QuickTeach™ and AI Path Optimization empower any cobot champion to quickly become a high-speed cobot wizard. These powerful tools are included free on every new Vectis Cobot Welding Tool. QuickTeach and AI Path Optimization are also available for retrofit to existing Vectis Cobot Welding Tools Teach directly at the cobot’s wrist with Vectis Automation’s QuickTeach puck, allowing for fewer keystrokes per weld — further lowering the batch-size threshold and operator skill level required.
The AI Path Optimization software then applies your specified work angle and travel angle, mitigating effects of any human error during teaching. Sharp corners are automatically detected and smoothed for consistent, quality welds.
Advantages of the QuickTeach and AI Path Optimization:
- Reduced programming time: Smaller viable batch sizes and higher per-batch ROI.
- Consistent weld angles: Higher quality welds for all skill levels.
- Automatically smoothed wraps and corners: Less “tribal knowledge” required for successful programs; plus, higher quality corner welds.
At IMTS 2024 in Chicago, Vectis Automation demonstrated its Park’N’Arc range extender for welding applications featuring the UR20 cobot from Universal Robots.