Advancements in Cutting Systems Transform the Manufacturing Landscape
Faster cutting speeds, and advances in software and automation capabilities expand the versatility of metal cutting systems.
Posted: November 16, 2024
Laser, plasma, oxyfuel and waterjet cutting systems each have their own strengths, and the choice of cutting method depends on the material being cut, the desired precision, and the production speed required. Here’s a look at recent innovations.
Plasma Cutting System Pays Back with Versatility, Productivity and Precision
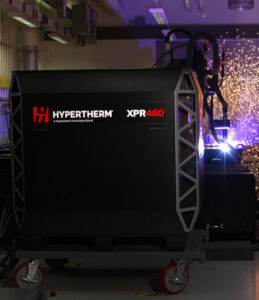
Positioned as the newest addition to the XPR line with X-Definition technology, the Hypertherm® XPR460® plasma cutting system is an advanced plasma system that pays you back with maximum versatility, productivity and precision.
With enhanced thickness and speed capabilities, the XPR460 from Hypertherm Associates (Hanover, NH) sets a new standard for precision and productivity. The system delivers superior performance in cut quality, thickness capacity, and cutting speeds. It ensures consistent part quality from the initial cut to the last, delivering superior cutting versatility for mild steel, stainless steel and aluminum.
SureCut technology optimizes Hypertherm plasma performance by automatically embedding advanced cutting capabilities and delivering improved customer outcomes. The system’s optimization for productivity and cost-efficiency extends to its ability to maintain exceptional cut quality on 45° bevels and ensure uniform hole aesthetics throughout.
With arc response technology, the XPR460 is engineered for system optimization. Ramp-down error protection significantly increases realized consumable life, and torch protection reduces the impact of catastrophic electrode blowouts, which can damage the torch at high current levels.
Designed for seamless operation, the XPR460 features Argon-assist technology for effortless extended piercing capability and edge-starting on thick mild steel and stainless steel. Additionally, its advanced process control mechanisms prioritize plate protection and consumable efficiency, minimizing downtime and maximizing output.
With four gas-connect console options, the XPR460 offers unparalleled flexibility and control over the cutting process. Each console is seamlessly integrated with the CNC interface, ensuring ease of use and high productivity. Moreover, CorePlus, VWI, and OptiMix gas-connect consoles enable improved marking applications, enhancing the system’s versatility and efficiency.
New Automation Solutions and an Expanded Customer Service Network
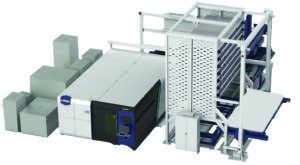
HSG Laser’s TPSD is an all-in-one tube laser cutting solution that combines cutting, tapping, and drilling in a compact, efficient machine.
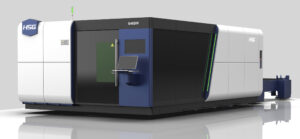
HSG Laser’s GV+Tower is a fully automated 2D laser cutting system designed for large-scale production environments and features a powerful 60 kW fiber laser.
At FABTECH 2024, HSG Laser (Addison, IL), a global leader in metal shaping equipment and automation solutions, unveiled an ambitious U.S. expansion strategy with the launch of three advanced automation solutions, alongside enhancements to its customer service network.
Among the automation solutions are the GV+Tower, a fully automated 2D laser cutting system designed for large-scale production environments. Featuring a powerful 60 kW fiber laser, the system can cut materials up to 3.9” thick, offering speeds up to 400% faster than traditional 12 kW systems.
The GV+Tower integrates advanced automation features, including automated material loading and unloading, to reduce manual labor and boost productivity. Its seamless integration into existing production lines makes it an ideal solution for manufacturers seeking high-speed performance with an affordable initial investment.
Also at FABTECH, HSG also introduced its all-in-one tube laser cutting solution, TPSD, which combines cutting, tapping, and drilling in a compact, efficient machine. Designed for industries such as fitness equipment, furniture, and job shop manufacturing, it accommodates tube sizes ranging from 0.47”-to-10” in diameter.
With intelligent automation, the TPSD helps manufacturers reduce material waste, production time and labor costs. This versatile solution offers a cost-effective approach to handling complex geometries with high precision.
Also featured at FABTECH was the HLGW Robo, a collaborative robot laser welding system developed by HSG Japan. It is especially designed for industries with small to medium lot sizes. The HLGW Robo offers exceptional flexibility, capable of handling a wide range of welding tasks with ease. Its integration with HSG Japan’s advanced laser technology ensures efficient, high-quality, and safe welds, minimizing material distortion and enhancing overall production quality.
In addition to the product launches, Mitsubishi HC Capital America and HSG Laser are partnering to provide clients with enhanced financial support, further solidifying HSG Laser’s position in the U.S. market. Since entering the market in 2020, HSG Laser has steadily increased its presence by delivering high-performance fiber laser cutting systems. The strategy allows for localized solutions, fast-response service, and a robust support network.
High-precision Plasma Machine Offers Most Affordable Option in Market
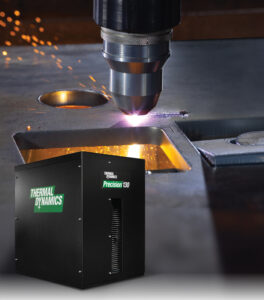
Thermal Dynamics® Automation’s (West Lebanon, NH) Precision 130 high-precision plasma system, which features a 130-amp power source and a water-cooled torch rated for piercing and production cuts on 20 mm mild steel, stainless steel and aluminum. The Precision 130 offers the same superior cutting performance as Thermal Dynamics’ UC 131 but in a system that is more compact, streamlined and affordable. The Precision 130 is fully compatible with Thermal Dynamics iCNC Performance controller and Intelligent Height Controller (iHC).
“We designed the Precision 130 for users with smaller tables and for those who want to step up from conventional to high-precision plasma cutting,” said Dirk Ott, vice president, Global Mechanized Plasma Systems for Thermal Dynamics Automation. The Precision 130 measures 20”-x-30”-x-34” and can be positioned close to a table when there is limited space available.
Compared to other high-precision plasma power sources that require multiple components (power source, remote arc starter, gas control boxes), the Precision 130 offers the advantage of a complete system with one main enclosure and a very small gas controller. It can cut using all popular high-precision plasma/shielding gas combinations, including Air, O2, N2, H35, H20 (water mist secondary process to optimize non-ferrous cutting) and air/air to lower cutting costs on mild steel. However, only a single plasma/shielding gas combination is possible at a time.
The Precision 130 system has a cutting output of 130 amps at 1000% duty cycle. It cuts ¾” steel at 52 IPM (20 mm at 1,321 mm/min) and ½” steel at 85 IPM (12 mm at 2,159 mm/min). It has a maximum cut capacity of 1-1/2”). Like the UC 131, the Precision 130 features a 130-amp Thermal Dynamics XT torch with its SpeedLok consumables cartridge, which allows users to change consumables in seconds. The maximum torch lead length is 50’.
The Precision 130 can be driven using the TD System Interface App (available in the Apple App store or on Google Play), which offers system process and troubleshooting controls and makes it possible to easily upgrade old cutting tables whose numerical control cannot handle complex communication protocols.
Faster, More Accurate Waterjet Cutting While Reducing Downtime

the industry’s most advanced
waterjet machine, providing faster and
more accurate print to part cutting while
reducing downtime.
Designed and manufactured by Hypertherm Associates (Hanover, NH), a U.S.-based manufacturer of industrial cutting systems and software, the OMAX® OptiMAX® is the industry’s most advanced waterjet machine, providing faster and more accurate print to part cutting while reducing downtime.
The culmination of three decades of OMAX engineering expertise and user experience, the OptiMAX is designed for manufacturers in need of a versatile, easy-to-use cutting system to increase the capability and efficiency of their operation. It offers OMAX IntelliMAX® intuitive software for optimized cutting capability and power, along with enhanced automation to maximize uptime so users can deliver finished products faster. Features include:
- IntelliMAX premium software, designed for incredible ease of use and operation quickly following installation. Incorporating decades of proprietary waterjet cutting models, no other system can consistently produce parts as rapidly or capably.
- IntelliVISOR® console with key metrics to optimize operations and complete system monitoring that helps avoid unplanned downtime.
- EnduroMAX® pump that automatically sets the correct pressure and minimizes fluctuations to improve component life, while offering the most efficient waterjet pump technology in the market.
- IntelliTRAX® drive system with advanced motion control for further increased system robustness and reliability. Virtually no maintenance is required compared to more conventional ball screw and rack and pinon drive systems.
- New garnet delivery system to further minimize downtime.
- Combined with an optional TiltaJET® taper compensation head, the OptiMAX waterjet line is the most accurate system on the market.
“The OptiMAX represents the pinnacle in abrasive waterjet cutting,” said Arion Vandergon, waterjet product marketing manager for OMAX. “It builds upon everything the OMAX team has learned over the decades to deliver the most capable and efficient waterjet cutting system available today enabling optimal cutting outcomes for our customers.”
Laser Cutting Made Easy with the new ByCut Eco
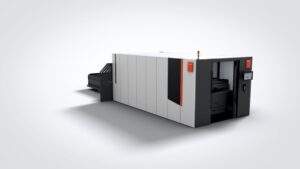
The ByCut Eco by Bystronic, Inc. (Hoffman Estates, IL) is distinguished by its efficiency as well as its simplicity: expert and novice users alike will find it both easy to navigate and operate. The new ByCut Eco is the fiber laser for getting started and hitting the ground running, which makes it the attractive laser cutting system for successful sheet metal processing. With up to 6 kW of fiber power, a broad range of materials can be processed, from steel and stainless, to non-ferrous metals such as aluminum, copper and brass.
The simplicity of the user interface, which utilizes a full 21.5” touch screen display and the powerful BySoft Cell Control Cut, enables users to operate, nest parts, and optionally create their own parameters with the Parameter Wizard. It’s as easy as operating your cell phone.
Laser Cutting Machine Generates Bevels While Cutting, Reduces Downstream Processes
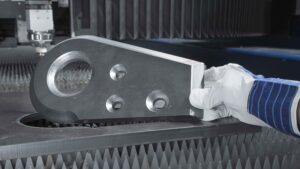
The TruLaser Series 3000 Bevel Cut Edition also produces complex bevel geometries and countersinks without problems.
The TruLaser Series 3000 Bevel Cut Edition from TRUMPF Inc. (Farmington, CT) can produce beveled cutting edges (chamfers) on the top and bottom edge of the component while cutting. This ensures optimum preparation of the welding edges and reduces downstream processes. The machine can apply chamfers to sheets of up to 1” thick and handle complex bevel geometries with ease. The TruLaser Series 3000 Bevel Cut Edition solution is particularly suitable for mild and stainless steel.
“With the TruLaser Series 3000 Bevel Cut Edition, manufacturers have a particularly productive universal machine with which they can integrate downstream process steps into laser machining,” said Grant Fergusson, TRUMPF Inc. TruLaser 2D laser cutting product manager. “Thanks to the unique design of the cutting unit, the machine can create chamfers of up to 50°, depending on the sheet thickness, which is more than the 45° that were previously standard in the industry.”
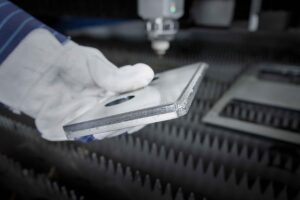
The TruLaser Series 3000 Bevel Cut Edition optimally prepares welding edges by automatically generating beveled cut edges on the contours of parts while cutting.
For this solution, TRUMPF has equipped the cutting unit of the TruLaser Series 3000 Bevel Cut Edition with two additional rotary axes, ultra compact drive motors, and a nozzle specifically developed for bevel cutting. Thanks to the special design, the cutting head can be tilted in all directions up to an angle of 50°. As usual, the cutting unit regulates the distance to the sheet, minimizing the risk of collision despite the steep angle. The TruLaser Series 3000 Bevel Cut Edition also comes equipped with TRUMPF collision protection, to further guarantee process reliability and prevent structural damage by avoiding collisions with tipped parts.
Due to the cutting unit’s high flexibility, users can create bevels in different geometries. In addition to the classic V and Y edges, edge geometries in which both sides of the part edge are provided with bevel cuts, also known as double V (DV) edges or X prep and double Y (DY) edges or K prep, are possible. This edge-geometry flexibility is advantageous when complex parts or groups of parts must be welded.
To meet the high demands required to prepare complex bevel cuts, TRUMPF has developed a new, particularly simple, and intuitive programming system. It contains a preselection of all the processing strategies, which the user can flexibly adapt as required. There are also predefined cutting parameters for the special bevel cut nozzles. This does not reduce the high productivity of the TruLaser Series 3000.
For 2D processing of components without bevels, the machine is equipped with all of TRUMPF’s proven laser cutting features, such as Highspeed Eco for gas consumption reduction, FlexLine for the reliable processing of different material grades, and EdgeLine Bevel for the rounding of the upper sheet edges.
The TruLaser Series 3000 Bevel Cut Edition was scheduled to make its North American debut at FABTECH 2024.
Fiber Lasers and Automation Lower Costs and Ensure Predictable Production Schedules
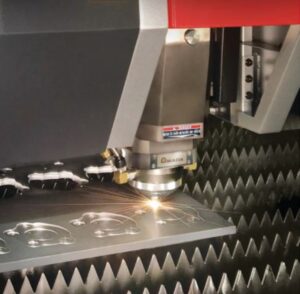
AMADA AMERICA INC.’s (Buena Park, CA) VENTIS 3015 AJe fiber laser was recently paired with AMS CLT automation and TK 3015L automated parts sorter at FABTECH 2024. This system combines AMADA’s revolutionary Locus Beam Control (LBC) to achieve infinite locus patterns to ensure optimum beam shape control for each specific cutting application with 24/7 processing capabilities. The LBC achieves infinite locus patterns to ensure optimum beam shape control for each specific cutting application. The LBC technology delivers unprecedented high-speed and high-quality cutting up to three times faster than a conventional fiber laser.
A high-brightness fiber laser oscillator maintains optimal quality of the high-energy density laser beam. As a result, VENTIS provides virtually dross-free cutting of a variety of materials and thicknesses including stainless steel and aluminum.
Productivity Mode: In the N2 non-oxidizing cutting of medium-thick stainless steel and aluminum, processing cost can be reduced by up to 75%.
Quality Mode: Cut quality is ensured by reducing the surface roughness by approximately 50% when compared to a conventional machine and dross is reduced to less than 10 μm.
Kerf Control Mode: Enables long-term stable processing during automated system operation. By oscillating the beam, the kerf width can be controlled to 2.5 times wider than a conventional machine.
The AMS 3015 CL provides a flexible automation solution that reduces unnecessary machine downtime due to manual material loading. Manufactured with precision in Brea, Calif., and High Point, N.C., the AMS CL automatically and consistently performs material handling operations to maximize machine productivity. This modular system allows fabricators to easily expand their automation capabilities. With additional modules, the AMS CL can seamlessly transition from a single-cycle loader to a multi-shelf tower that can support multiple lasers. Asymmetrical design allows modules to be placed on either the front or rear side of a laser’s shuttle table to accommodate material flow.
The TK 3015L Automated Parts Sorting Cell is designed to unload everything from the most intricate part nests to large panels. As laser nests are typically programmed with parts for different jobs, the TK-L optimizes downstream processes making production more efficient and profitable. The TK-L minimizes the chance for errors to occur during downstream operations by stacking parts according to the next phase in production.
Flex Machine Tools Partners with IGEMS to Elevate Waterjet Cutting

Flex Machine Tools (Wapakoneta, OH), an American manufacturer and leading provider of machine tool solutions worldwide for metal fabrication operations and more, has partnered with IGEMS of Sweden to integrate the FlexJet Waterjet Series with IGEMS CNC control, CAD/CAM software and hardware.
Known for its precision and versatility, the FlexJet Series now features enhanced capabilities due to IGEMS’ software and hardware such as the advanced Tilter 5-axis waterjet cutting head, Snapper camera for optimal positioning, Rounder kinematic compensation tool, and Straighter perpendicular angle tool. These improvements are designed to cater to the intricate needs of diverse materials and cutting requirements, ensuring unparalleled accuracy and efficiency in waterjet cutting processes. Adding to the technological advancements, the FlexJet will also be equipped with IGEMS’ HMI and Beckhoff’s state-of-the-art industrial PC. This integration signifies a significant leap in operational control and user experience, offering intuitive interfaces and robust performance that redefine industry standards.
With this partnership, customers in North America can expect to experience enhanced cutting performance and increased productivity, thereby transforming their operational capabilities.
“By combining IGEMS’ exceptional software with Beckhoff’s leading-edge hardware on our FlexJet machines, we are setting a new benchmark for precision, efficiency, and reliability in waterjet cutting technology,” said Don Kemper, president of Flex Machine Tools. The collaboration between Flex Machine Tools and IGEMS is a testament to both companies’ dedication to technological advancement and customer satisfaction.
New BevelArc 3D Increases Cutting Reach Capability to 90°
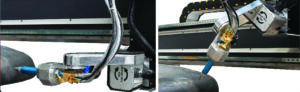
The new BevelArc 3D from Tecoi USA (Longview, TX) adds an additional axis, increasing the cutting reach capability of their line of plasma, oxyfuel, and laser plate processing machinery. With it, cutting heads can now be positioned from 0° to as much as 90° from a vertical position, providing more efficiency than other systems. This expanded cutting head reach capability is especially important for cutting and fabricating pressure vessel tank heads — as well as cutting difficult shapes and profiles from beams, plates, and tubes.
With the BevelArc 3D, users can perform continuous beveling by tilting, without unnecessary torch turning. Since the torch does not have to move, it is not necessary to make loops to recover torch position, except in rare cases where the finishing of the corners requires it. Unlike most bevel heads limited to +/- 45°, the BevelArc 3D provides a real advantage for cutting shapes that typically cannot be processed on typical thermal cutting machines.
Other advantages of the new Tecoi BevelArc 3D are easy operation and adjustment, automatic restart after collision, automatic proportional height control, and high precision roller runners. The BevelArc 3D can be easily adapted to any Tecoi USA plate processing machine.
Tecoi USA designs and manufactures customized large format plate processing solutions that integrate oxyfuel, plasma, and laser cutting processes with machining and material handling. Tecoi USA serves a wide array of companies and industries comprising a wide range of sectors in metal processing including steel service centers, steel construction, heavy duty machinery, the oil and gas industry, shipyards, and for wind power.
Large-size Turret Punching and Laser Cutting in a Single Compact Space
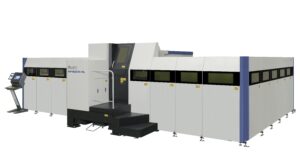
The MF30510HL, a multifunction machine that combines turret punch press and fiber laser processes, is designed to meet the evolving needs of modern manufacturers. Developed by Murata Machinery USA Inc. (Muratec) (Charlotte, NC) in response to customer requests for a machine to process larger sheet sizes than the popular MF3048HL, the MF30510HL features an expanded work size of 5’-x-10’ (1,219-×- 2,438 mm) and a punching capacity of 30 metric tons, offering unparalleled versatility in processing larger material.
The MF30510HL streamlines operations by merging punching, laser cutting, forming, tapping, deburring, and more into one cohesive machine. Its 4.0 kW fiber laser output enables the efficient processing of a wide range of sheet materials and thicknesses. Integrating with Muratec’s automation systems, including the FG series parts-sorting system, it further enhances production efficiencies.
Key features include:
- Integrated Four-Station Rigid Tapping Unit: A four-station rigid tapping unit that enhances operational versatility, efficiency, and high-speed tapping operations.
- Vibration-Free Laser Operation: The fiber laser remains securely mounted on its dedicated frame, eliminating potential vibration interference during cutting and punching operations. This deliberate design ensures unparalleled precision and consistency in processing results.
- Retractable Bottom Dies: This function retracts forming dies when not in use. This allows the machine to perform laser cutting and punching operations to reduce the chance of scratching and catching while making adjacent punch stations available.
- Process Net Monitoring: Accelerates real-time monitoring and control for fiber laser operations and provides operators and manufacturing managers valuable insights. Operators can make informed decisions, optimize settings, and ensure optimal performance, productivity, and quality.
To further enhance the MF series, the tooling styles of Wiedemann 114 and Thick Spring Style turrets are able to accommodate your present machine’s tooling inventory. This combination machine can also be seamlessly paired with unmanned automation for loading and unloading, and with the FG series, Muratec’s next-level parts sorting system to enhance production efficiency.
Muratec’s legacy of leadership in sheet metal fabrication is rooted in the Wiedemann Machine Co., a pioneer in the industry since 1916. In 1989 Murata acquired the Wiedemann brand, merging their expertise to create Murata Wiedemann.
Empowering Efficiency with Enhanced Features: ProNest Nesting Software
Hypertherm Associates (Hanover, NH), a U.S.-based manufacturer of industrial cutting systems and software, offers a major version update to ProNest 2025 version 16.0 nesting software. There is a collection of new features and ongoing updates designed to help customers improve their operational efficiency while reducing non-value-added tasks.
New features include the following:
- Enhanced integration with Tekla® PowerFab® Connector this optional module provides seamless data exchange between ProNest and Tekla PowerFab.
- Library parts update ensures the latest revision is always available.
- Job auto recovery helps save work in progress from being lost.
- Collision avoidance, now included by default in ProNest LT for OMAX waterjet setups, ensures an optimized cut path is applied in ProNest, eliminating the need for secondary steps in IntelliMAX.
Other recent features and enhancements:
- Crop line improvements include multiple crop lines per nest with capabilities to cut empty plates using crop lines, change cut direction and apply XY coordinates.
- Small entity detection identifies motions that are smaller than kerf width or other length value, which can cause errors at the machine or may result in poor cut quality.
- Machine home movement moves for remnants that do not have a corner at the standard machine home.
- Setting improvements vaporizes for laser machines that support this capability.