Future-ready Crane Production: Liebherr Invests in Metal Processing System
Automated deburring line frees up employees at Liebherr-Werk Biberach GmbH from monotonous and physically demanding work. Machine aids the production of high-quality tower cranes and mobile construction cranes.
Posted: September 24, 2024
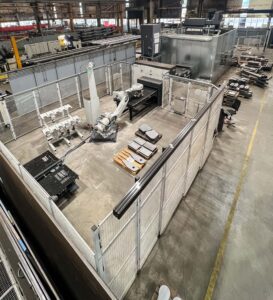
An innovation that is a world first of its kind: the new deburring line for cut parts at the Liebherr production site in Biberach. Working with specialists from ARKU Maschinenbau GmbH, Rösler Oberflächentechnik GmbH and Teqram B.V., Liebherr-Werk Biberach GmbH has automated the edge rounding of plasma, oxyfuel and laser-cut metal sheet. In doing so, the company is making the
Removing slag, descaling, deburring and rounding edges: the new system does it all. This means that metal sheet weighing up to 200 kilograms can be optimally prepared for subsequent production steps. The parts are then turned into components for crane jibs and tower sections. Robots with state-of-the-art camera technology position the sheets, which are up to 1,250 millimetres wide and 100 millimetres thick, and remove them again after processing.
“Until now, edge-rounding work has always been done manually,” says Robert Piesche, Production Technology Engineer at Liebherr-Werk Biberach GmbH. Despite high safety standards being in place, there was still a certain risk of accidents happening with this job and its use of angle grinders. “Automating processes means we can free up employees from monotonous and physically demanding work. They are also exposed to less dirt and noise as a result and we have been able to significantly increase occupational safety.” The new deburring line also plays a key part in the production of high-quality tower cranes and mobile construction cranes.
Experienced partners in metal processing and robot technology
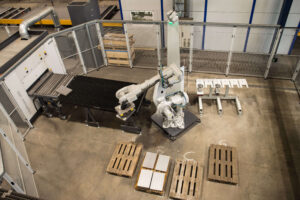
Liebherr brought together three experienced partners in the field of metal processing and robot technology, ARKU Maschinenbau GmbH, Rösler Oberflächentechnik GmbH and Teqram B.V., with a view to fully automating the work processes. “This set-up, as it exists at our plant, is the first to bring together components from this trio of companies,” explains Dominic Kreutle, Head of Production Technology at Liebherr-Werk Biberach GmbH. One of the biggest challenges lay in achieving a smooth integration of the various system interfaces.
The robot systems with various grippers are supplied by Dutch experts Teqram B.V. Equipped with intelligent cameras, the ‘EasyBots’ can recognise parts in their work area independently and regardless of their position on the pallet. This means that the usual time-consuming teaching or programming of each robot is no longer necessary. The robots also have a option of automated processing for parts that are too large for the line. With access to various tools such as chisels and angle grinders and their advanced camera and sensor technology, they are capable of finishing parts with precision.
Line production meets highest quality standards
The Bavarian company Rösler Oberflächentechnik GmbH supplied the wire belt blasting system for descaling, paint stripping, derusting, roughening and cleaning the sheet metal. This delivers all-round, thorough and always reproducible blasting quality. The system for deburring and edge rounding (the EdgeBreaker® 9000) was manufactured by ARKU Maschinenbau GmbH, based in Baden-Baden. This enable efficient slag removal, deburring and rounding of sheet metal in a single run. Compared to single-sided machines where sheets have to pass through several times, this system cuts time by 50 per cent and also increases productivity.
Liebherr consciously chose European manufacturers, not just because of the quality of their products, but also because of their comprehensive customer service. This strategic decision reflects Liebherr’s commitment to ensuring the highest standards of quality and operational efficiency.
The companies involved voiced their enthusiasm during a tour of the finished installation. “We are pleased that our system for slag removal, deburring and edge rounding offers a suitable solution for economical line production that meets the highest quality standards,” said Stefan Sauter, International Sales at ARKU Maschinenbau GmbH. Vasili Schaermann, Global Sales Expert at Rösler Oberflächentechnik GmbH, added, “Our blasting system fits perfectly into the production process and delivers impressive results.”
The shortage of skilled labour was also a key point of discussion during the tour. “In times when skilled labour is in short supply, our robot technology can be a crucial component in closing this gap and making work steps more efficient,” said Markus Lindörfer, Automation Specialist at Teqram B.V. Liebherr was finding it increasingly difficult to recruit qualified employees for this area. The deburring line was planned over an extended period of time, with the reduced need for labour being considered early on in the process. Employees have been able to take on other roles at the production site in Biberach.
Investment despite crisis
The three manufacturers have already worked together several times in various ways, which had a positive impact on the project at Liebherr. “Communication between the companies involved has been outstanding. Everyone considered each other so we were able to achieve progress quickly,” says Robert Piesche. The system went into operation in May of this year and has been running reliably ever since. This project reflects Liebherr’s investment in its Biberach site despite difficult economic conditions.