Turbocharge the Industrial Cleaning Process with Laser Robotic Work Cells
The advances in today’s industrial laser cleaning automation are revolutionizing the way metalworking companies handle rust and contaminant removal, as well as conduct surface preparation, particularly when it comes to high volumes of component parts and equipment. Combining lasers with…
Posted: August 22, 2024
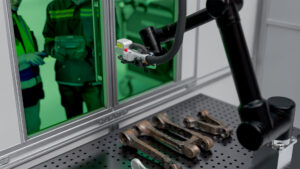
The advances in today’s industrial laser cleaning automation are revolutionizing the way metalworking companies handle rust and contaminant removal, as well as conduct surface preparation, particularly when it comes to high volumes of component parts and equipment.
Combining lasers with advanced robotics in enclosed work cells marks a significant leap in industrial cleaning capabilities. Operators are able to efficiently and repeatedly clean components of different sizes, shapes, and materials at a level previously unattainable through manual methods.
“Automated laser cleaning systems are designed to cost-effectively clean high volumes of even the largest format parts and equipment and can be tailored to suit the size and complexity of the parts, while eliminating concerns over operator safety,” said Wayne Tupuola, CEO, Laser Photonics.
Surpassing Manual Cleaning and Preparation Solutions
Metalworking shops are constantly removing corrosion, grease, residue, and old coatings from metal, or they need to roughen the surface of the metals prior to coating components and equipment. What’s more, contaminants or toxic substances often need to be eliminated before further processing of the metals.
Conventional removal methods such as sandblasting, dry ice blasting, and chemical stripping are messy, and time and labor intensive. The processes require preparation and cleanup, as well as require costly consumables. These processes also pose risks to applicators and the environment, and are closely watched by regulators, including OSHA and the EPA.
A more efficient cleaning and surface prep method can be found by implementing laser cleaning robotic work cells. These efficient alternatives to conventional removal methods typically consist of at least one laser-wielding robot, controllers, and safety equipment in see-through enclosures. These collaborative robots, or cobots, excel at tasks such as the laser cleaning of parts which involve repetition. The implementation of cobots frees up employees to work on other activities within the shop.
The CleanTech Robotic Cell from Laser Photonics, as an example, uses a robotic arm to grip a laser gun that conducts cleaning, roughening and finishing functions. Operators program these robotic arms via a tablet/controller, inputting the coordinates for material processing. Additionally, the cleaning laser can be replaced with a welding or cutting laser. To address various challenges and enhance efficiency, work cells can be split into two sections. On one side, the robot performs cleaning tasks; while an operator installs a part to be cleaned on the other side. “The operator can lay out several components for cleaning over the flatbed, set the cleaning coordinates, and leave the robot processing,” Tupuola explained.
He credited the advancements in laser technology that are behind the acceleration of the efficient cleaning of such shapes. “Dual axis laser technology enables the cleaning of target areas more effectively and quickly if they are complex and uneven. Plus, our proprietary technologies allow the laser to move in various directions and clean hard-to-reach areas.”
Metalworkers that manufacture large format components will find systems, such as the CleanTech Titan FX, offer a work envelop up to 6’-x-12’ to perform automated laser cleaning, rust removal and surface conditioning. Such a system operates as a standalone unit or can be easily integrated into a production line environment.
“Large format automated laser cleaning systems can expedite the processing of [applications like] automotive tire rims, molds, oil and gas flanges, or even sheets for the hull of a ship or other vessel,” Tupuola said. The size and configurations of enclosures can be customized to accommodate various part sizes, and lasers can operate at a range of power levels.
Safe and Secure
Among the many benefits and advantages of laser cleaning automation is improved level of safety to both operators and the environment. “For extra safety, our custom-tailored automated laser systems are enclosed in a Class I safety work cell,” Tupuola said. “We can also integrate dust and residue collection, as well as a fume extractor that captures vapors during the cleaning of toxic substances.”
The integration of advanced cleaning equipment in industrial settings not only enhances efficiency but also ensures adherence to stringent safety and waste management regulations and guidelines such as those issued by OSHA and EPA. Advanced laser cleaning systems are designed with these considerations in mind, offering businesses a reliable solution to meet compliance standards.
Conventional cleaning systems, such as abrasive sandblasting involves forcefully projecting a stream of abrasive particles onto a surface, usually with compressed air or steam. The silica sand used in the process fractures into fine particles and becomes airborne, which can cause serious or fatal respiratory disease. What’s more, particles that result from removing coatings, as an example, can also be inhaled. To avoid breathing in particulates, operators must wear full HEPA suits when sandblasting.
And with chemical removal processes, where chemicals are used to strip metal-based objects of paint, rust, and other contaminants operators can be exposed to corrosive acids and noxious chemical fumes. What’s more the disposal of chemicals is costly and closely regulated.
Laser cleaning seeks to solve or minimize the issues associated with abrasive sandblasting and chemical removal processes. An advantage to laser cleaning systems is that they require no consumables other than electric power, minimal labor and minimal maintenance.
The implementation of industrial-grade robotic laser cleaning systems offers substantial long-term benefits that enhance their value proposition for metalworking shops, supported by longevity, low maintenance, and a high return on investment.
Effortless Programming
Programming the laser ablation procedure with a cobot work cell can be accomplished with a touchscreen. Generally, programming includes setting coordinates for the sample, ablation pattern, power output, and cleaning speed, Tupuola said.
“Installation and programming are needed, but once it’s set up, robotic cell cleaning is fast, precise, thorough and controlled. So, it’s a very convenient, optimized process if the parts being cleaned are the same.”
On the horizon regarding these industrial cleaning systems is the implementation of 3D scanners into the robotic work cell, which would automate the focusing of the laser and eliminate some of the programming currently required.
Precision laser-based systems, while efficiently used to clean industrial surfaces, typically require manual labor to remove rust, contaminants, and so forth. Automated robotic laser cleaning systems provide manufacturers with safer, easier, and more eco-friendly options.
As manufacturers strive to meet increasing demand efficiently, the adoption of advanced laser cleaning systems is becoming more prevalent across various industries. These systems offer cost-effective, high-volume cleaning with the precision and speed necessary to stay competitive for decades to come.