Securing the Long-term Success of the Metalworking Sector
Closing the skills gap in the metalworking industry future proofs the long-term success of the industry.
Posted: August 22, 2024
Companies involved in the metalworking industry continue to do their parts to ensure the future of the manufacturing workforce, be it through donations or through partnerships and collaborations with high schools and higher education institutions.
Welding Student Invites Hypertherm Associates to High School Graduation
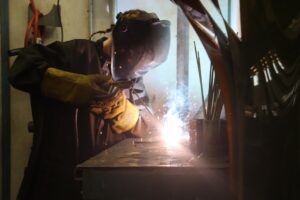
What’s the perfect gift for a high school graduating senior? In response to receiving an invitation to 17-year old Autumn Mayo’s Sitka, Alaska, high school graduation, Hypertherm Associates (Hanover, NH) sent her a Powermax45 XP complete with cartridges, and a signed copy of famous metal artist Rae Ripple’s book When I Grow Up.
“At Hypertherm, we believe in what Autumn and her teachers are doing,” said Stephen Bruner, regional marketing & revenue operations director for Hypertherm. “Autumn is a perfect example of the students we’re trying to reach and support through our company’s mission.”
Mayo’s journey into welding began in her high school’s metal shop and welding classes, where she developed her skills under the mentorship of her teacher. Having successfully completed courses in metalwork, engines, arc welding and plasma cutting, Mayo is preparing to further her education at the Universal Technical Institute in Arizona this fall. Like many students attending trade schools, Mayo will be responsible for supplying her own tools, which can be expensive. In her search for the best equipment, she discovered Hypertherm’s plasma cutting technology.
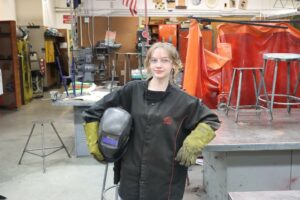
“When I attend school in Arizona, we have to bring some of our own gear,” Mayo said. “So, I researched companies that had good supplies and saw Hypertherm. They just stuck out.”
Mayo is a part of the growing number of high school students who are focusing on career and technical education programs, a number which Hypertherm is focused on nurturing. The Bureau of Labor and Statistics reports that the number of female welders has soared in recent years. Their numbers indicate that between 2016 and 2019 there has been an increase of 30% of women in the welding industry. Even with that increase, in 2020, women welders only made up 3.8% of the welding industry, and today they account for a little more than 6% of welders. Brunner added, “One way we are addressing the skilled labor shortage is by committing to this next generation of the workforce with our Spark Something Great grant. It helps those schools by providing a versatile system instructors can use to teach handheld and mechanized cutting, as well as applications such as gouging, flush cutting and marking. We wish Autumn nothing but the very best in her next chapter and are happy to be part of her future success.”
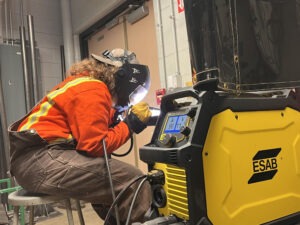
ESAB Boosts Technical Education with Welding and Cutting Equipment Donation to Hanover High School
Through its Future Fabricators program, ESAB (North Bethesda, MD) has donated welding and cutting equipment with an approximate retail value of $23,000 to support the welding technology program at Hanover High School in Hanover, Pa. The equipment included five Rebel™ EMP 205ic AC/DC multi-process and five Rebel 285ic 120v-230v 1ph welding machines and carts, a manual plasma cutter, five Sentinel helmets, and 10 Savage A40 helmets. ESAB’s Hanover facility was established in 1968 and employs more than 250 people between its welding filler metal production facility and training center.
“ESAB has collaborated with Hanover High School for many years to support workforce development needs in the Hanover community,” said Eleanor Lukens, ESAB President of the Americas. “Our most recent welding and cutting equipment donation ensures that students will be able to develop their skills using the types of welding and fabrication technologies that they will find in the industry. There are many career pathways available in welding. By working with schools and students through the ESAB Future Fabricators Program, we are supporting a workforce that is better prepared to pursue careers in manufacturing- and fabrication-related programs.”
Lukens noted that welding careers are in high demand. According to the American Welding Society welding workforce data, U.S. industry needs 330,000 new welding professionals by 2028.
The welding technology program at Hanover High School is a Pennsylvania Department of Education – Career and Technical Education Approved Program. Students enrolled in the program complete 720 hours of welding instruction during their 11th and 12th grade years. This includes hands-on welding in a welding lab with 10 booths, as well as theory-based instruction in the classroom. Students who are proficient or advanced can earn a NOCTI Certification (National Occupational Competency Testing Institute). In the 2023-2024 school year, 18 students were enrolled in the NOCTI program. In addition, 92 students were enrolled in Hanover High School’s Metals I, Metals II, and Metals III classes. These elective courses are typically taken by students in the 9th and 10th grade so they can gain experience.
“In addition to the donation of new machines, we are grateful for our partnership with ESAB for allowing our students to meet with individuals from the company to expand their knowledge and experiences,” said Dr. John A. Scola, superintendent of Hanover Public School District l. “By connecting with ESAB, they gain a broader understanding of the many career pathways that exist within the company. We have had the opportunity to tour the facilities and have individuals from the company visit our labs to work with students. We truly value this partnership as a district, as well as members of the Hanover community.”
OPEN MIND Technologies Joins Georgia Tech Manufacturing 4.0 Consortium
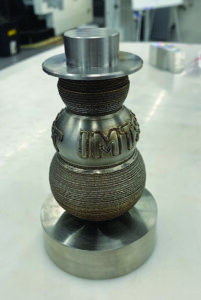
OPEN MIND Technologies (Needham, MA), a leading developer of hyperMILL® CAD/CAM software solutions worldwide, announced it has joined the Georgia Tech Manufacturing 4.0 Consortium. The consortium is a membership-based organization that facilitates key collaborations between industry, academia, and government to develop and deploy advanced manufacturing technologies as well as provide workforce development. Initial members have contributed funding, technology, and skilled resources supported by the staff at the Georgia Tech AI Manufacturing Pilot Facility located in Atlanta, Ga.
Alan Levine, managing director of OPEN MIND Technologies USA, said, “We are very pleased to join the Georgia Tech Consortium, which provides a great opportunity to participate in leading research and connect with other members focused on advancing manufacturing. The consortium offers a unique opportunity to expand OPEN MIND’s collaboration with Georgia Tech to the full membership and their specialized projects.”
“OPEN MIND’s commitment to the Manufacturing 4.0 Consortium and support of manufacturing education enables students to leverage top-tier CAD/CAM software for collaborative development of hybrid AM/CNC technologies,” said Kyle Saleeby, Manufacturing 4.0 Consortium’s research program director and research engineer at Georgia Tech. “Together, we look forward to pushing the boundaries of precision manufacturing.”
Consortium research projects cover an extensive range of topics that seek cost effectiveness, piloting new manufacturing systems, accelerating product development cycles, and adopting Industry 4.0 technologies.
Sandvik Coromant Centers: Unlocking Manufacturing Excellence
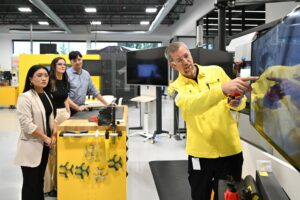
For the manufacturing industry, collaboration has never been more important. Navigating new technologies, global crises and the pressure to become more sustainable and productive can place a lot of weight on a manufacturer’s shoulders, and those working in the industry shouldn’t weather the storm alone. Fortunately, tailored processes, developed by seasoned experts, can pave the way for manufacturing success.
Since 2020, the manufacturing industry has risen to several challenges. Be it supply chain issues, geopolitical strife, talent shortage or economic instability, a successful manufacturer doesn’t batten down the hatches and go it alone. Instead, they look to their supply network to collaborate.
Knowledge sharing in manufacturing has never been more important. Take 2023’s Collin’s Dictionary Word of the Year for instance — AI. While awareness of the technology is high, many businesses remain unsure how to implement it.
According to Cisco’s AI Readiness Index, 84% of companies think AI will have a significant impact on their business, but just 14% feel ready to integrate it. As we navigate new technologies, no manufacturing business should go it alone. And it’s not just about AI — when dealing with any new challenge, collaboration is key.
For machine shop operators, there are many occasions where collaboration is best. For instance: when working with advanced materials that require specialized cutting techniques; when facing machining challenges, such as tool wear, vibrations or poor surface finish; or when optimizing toolpaths to maximize efficiency. The need for collaboration is where Sandvik Coromant Centers come into play.
Sandvik Coromant’s commitment to collaboration can be felt across the globe, with Sandvik Coromant Centers throughout Europe, Asia and the Americas, including Center Mebane in Mebane, N.C., providing dedicated hubs for product demonstrations and technical training. Customers can attend sessions to learn about a particular area of metal cutting, or about integrating digital machining solutions into their machine shops. From hardware to software, Sandvik Coromant Centers cover the whole manufacturing value chain.
Customers can also use one of the centers as a test environment. When dealing with complex projects, customers can trial new machining tools and strategies without disruption. Experienced experts guide every step to ensure project success, from tool selection and cutting parameters, to machine tool optimization and selecting the right coolant. Production processes remain uninterrupted, saving time and resources. With seasoned experts and advanced center capabilities, customers experience shorter development times, ultimately reducing resource and staffing costs.
Sandvik Coromant Centers are not only used as advanced testing facilities. They also act as a global network for metal-cutting expertise. The Sandvik Coromant Academy provides tailored and standard metal-cutting training, along with e-learning courses, closing the skills gap and future-proofing processes, taking a holistic approach and offering an enriching experience.
The Sandvik Coromant Academy is about so much more than teaching customers how to use Sandvik Coromant products. In 2023 alone, 36,000 learning interactions took place as a result of the academy’s work. Training sessions are developed with solutions in mind, whether that’s how to increase manufacturing productivity, reduce waste or make machining operations more cost effective. The training approach is less about instruction, and more about a holistic approach that acknowledges manufacturing challenges beyond machine use.
While physical training offers a wealth of benefits, the centers extend Sandvik Coromant’s knowledge to those who cannot visit in person through Digital Live Machining. With this feature, it is possible to remotely connect to actively participate in training and observe live machining without the need to travel. Customers can drive projects forward and tap into the full potential of the Sandvik Coromant Center without physical presence.
Sandvik Coromant’s approach to manufacturing resilience — Manufacturing Wellness — takes a holistic approach to the challenges the industry faces. We believe successful manufacturing companies deliberately do certain things. These include benefitting from strong partnerships and developing the workforce. For Sandvik Coromant, these are two healthy manufacturing habits we feel manufacturers should follow, and our Sandvik Coromant Centers, training academy and dedication to metal-cutting training help support that.
In 2024, collaboration will prove a key to success in the manufacturing industry. While the sector — and indeed the rest of society — faces a stream of ongoing challenges, there is also a wealth of opportunity. When greeted with new technologies and ways of working, coming together to unite expertise and harness the knowledge of one another will undoubtedly pave the way for a brighter, more resilient manufacturing future.- By Per Alfsen, global knowledge and center manager, Sandvik Coromant.