Improving Smiles Around the World with Help from ANCA CNC Machines
ENG-K turns to ANCA to support a 30% growth rate for their dental drill products.
Posted: August 15, 2024
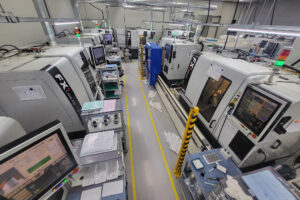
Jake Farragher, ANCA’s general manager for Asia, observes that dental drill manufacturing has taken off in the region. “Almost all of it is for export, including destinations far beyond Asia,” he explained.
ENG-K is a shining example. Established in Korea in 2014, they partnered with dental implant OEMs and began producing dental drills on CNC lathes. They soon added their first grinding machine, an ANCA FX7 Linear, in the second half of 2015. Since then, they’ve installed 14 more ANCA FX5 Linear machines to satisfy an annual growth rate of 30%. In fact, president Dae-Seong Kwak credits ANCA’s ability to deliver machines quickly as a key factor in their success.
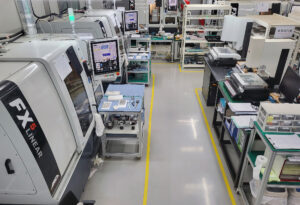
ENG-K actively participates with their client’s research and development of new instruments, thereby “satisfying the customer’s needs as much as possible by reflecting the function and structure in the production,” as Kwak puts it. ANCA also plays a role, he adds. “During the product development of our specialty tools and the R&D of our deburring tools and circular surgical tools, ANCA helped us a lot to improve our processes and quality. ANCA Korea supported our development of small diameter ball nose end mills, and we developed surgical cutting tools together with the help of ANCA’s headquarters in Australia.”
Multi-faceted automation
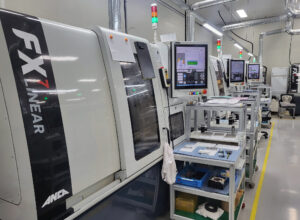
Profitably meeting customer demand for products like dental drills requires automation. Dental drills use a standard 2.35 mm shank size, explained Farragher, but the material is soft, so auto-loading risks marking the tool. “We integrated a pressure-reducing valve to grip dental drills a little softer than normal, and that opened up the market in grinding these products.” Kwak reported that ANCA’s drill loading system made them more efficient by increasing productivity and significantly reducing operator fatigue. “ANCA’s robot loader can be set up for more than 500 products in one batch,” enabling 24 hour “lights out” manufacturing, he added.
But truly automating production takes more than simply robot-loading the grinder. For example, Kwak points to ANCA’s internal wheel dressing feature. It adds to the overall cycle time, but “has the advantage of maintaining tool specifications” over a long production run, without the need for human intervention or an external wheel dresser.
Kwak also lauds ANCA’s automatic runout compensation. This system uses the standard Renishaw probe to check the tool blank in 3 planes, digitizes the actual centerline of the tool, and then compensates the entire kinematic to grind relative to that center, rather than the centerline of the work head. The resulting grind is nearly flawless, so no wonder Kwak says it’s been “very helpful” in the mass production of micro end mills.
Fast, secure setups
Kwak says ENG-K uses “both automatic and manual modes to produce customized products. ANCA machines have the advantage in either approach, because the operability of both automatic and manual modes is convenient and safe.” He credits ANCA’s latest software release with producing a high-quality tool radius and profile, making them “more competitive in the market.” And he applauds ANCA’s automatic warm-up routine, which he says has resulted in much less variability in grinding parameters. “Size deviations are smaller, so the defect rate is reduced and process reliability is assured.”
ANCA’s iBalance function has also proven to be another key setup feature. This option spins the wheel set at operating speeds and identifies any imbalance. If needed, the software tells the operator where to place threaded weights in the clamping nut in order to eliminate the imbalance. The process takes just 5 to 6 minutes per wheel set. Kwak reports that “iBalance is helpful in producing tight tolerance implant drills. Wheel life has also been increased by using this option.”
Kwak also praised the inspection panel in the software, saying it reduced measuring time during mass production and increased production volume. “It’s really good to be able to do in-process quality checks through the setup without the main door open. It has advantages for temperature changes and production.”
And in a final nod to their enduring partnership, Kwak enthused that “ANCA’s team in Korea has always managed to minimize production disruptions with friendly explanations and quick action. We’re very thankful.”