FABTECH 2024 Sneak Preview
From October 15-17, FABTECH will make its premiere showcase in Orlando, Fla., at the Orange County Convention Center. FABTECH is North America’s largest metal forming, fabricating, welding and finishing event. It is a one-stop venue where metal fabricators can meet…
Posted: August 22, 2024
From October 15-17, FABTECH will make its premiere showcase in Orlando, Fla., at the Orange County Convention Center. FABTECH is North America’s largest metal forming, fabricating, welding and finishing event. It is a one-stop venue where metal fabricators can meet with more than 1,500 world-class suppliers, discover innovative solutions, and find the tools to improve productivity and increase profits. There is no better opportunity to network, share knowledge and explore the latest technology. Gain insights into industry trends that will help you prepare for what’s ahead.
Expansion of Chiller Units for Laser Systems
Chase Cooling Systems (Washington, PA) has expanded the available sizes in its LASER SERIES line of chillers in time for FABTECH 2024. The company will be in Booth S-11050. The new largest size units, the QBE050-R TTM LSR and the CWE068-R TTM LSR, include the dual cooling circuits and individual pump features of the LASER SERIES that can be set to different temperatures. The overall cooling capacity of the LASER SERIES now ranges from 12 kW up to 65 kW. The newest units are designed to support 20 kW and 30 kW laser systems. Additional series features include adjustable fluid bypass, electronic hot gas bypass valve for tight temperature control, separate threaded fluid connections for laser and optics, RS-485 communications port and wheel kits. The series’ compact footprints allow users to get more out of a single unit. This series is truly designed with the unique requirements of the laser industry. Chase Cooling Systems anticipates this series to continue to grow in cooling capacity with two even larger units coming soon to their catalog.
Chase Cooling Systems provides quality industrial chiller equipment for a wide range of process cooling needs. Products are available to serve a variety of applications and industries. Process chillers range in cooling capacity from 0.5 ton to more than 350 tons. With both packaged process chillers and individual cooling accessories, Chase Cooling Systems has the unique ability to service every component in a cooling system.
Conventional Feed Line and New Advanced Graphical HMI Control for the Stamping Industry
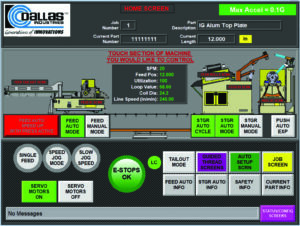
Dallas Industries (Troy, MI), a leading manufacturer of press feeding equipment and controls for the stamping industry will feature a conventional feed line and its new interactive and advanced graphical display control for press feed lines at Booth S-28003.
In a shared booth with AIDA-America, Dallas Industries will have a live demonstration of a conventional feed line running material on the AIDA servo press. The feed line will have Dallas’ unique software features within an Allen-Bradley controls structure. A large graphical display with simple-to-operate features will also be demonstrated.
The 15” new graphical display is designed to maximize productivity during start up and into production by providing an HMI touch and diagnostic screen for the entire feed line process. The new design features an intuitive and easy to follow graphical format that duplicates the machine in operation.
The new graphical display can reduce launch and set up time, minimize changeover time and assist production by providing real-time diagnostics for the entire machine.
Dallas Industries’ full line of products includes press feed lines in both conventional and SpaceSaver styles, a wide range of sizes and capacities of servo feeds, heavy-duty straighteners and coil handling equipment.
Live Cutting of the Fastest Fiber Laser in the World
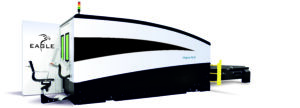
Visit Eagle Laser’s (Bonney Lake, WA) booth this year and see live cutting of the fastest fiber laser in the world, the Eagle iNspire®. Booth S-18129 will also have significant information regarding Eagle’s vast array of material handling automation. Eagle makes the most productive fiber lasers available, with models up to 13,780 ipm traverse, 6g acceleration, nine second pallet changer, and up to 30 kW of power. Eagle’s acceleration reduces cycle times on every part and allows the full power of the laser to be used on thinner material. With other lasers, the machine can’t move the head as fast as the laser can cut sheet metal, but the Eagle can. Eagle Laser – Nothing Faster.
Debut of Unique Automated Waterjet Cutting Capabilities
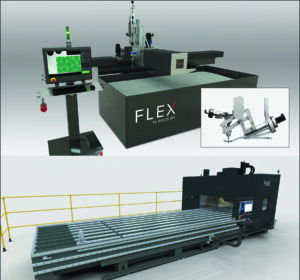
Bottom: FlexCNC G-Series GM-20-06 Vertical Machining Center.
Flex Machine Tools (Wapakoneta, OH), an American manufacturer and leading provider of machine tool solutions worldwide for metal fabrication operations and more, announced that at Booth S-22159 it will be demonstrating a range of high productivity manufacturing solutions for fabricators.
For the first time at a major North American trade show, Flex Machine Tools will have under power its innovative, automated waterjet solution. The precise FlexJet Waterjet FL-0404 is equipped with an IGEMS CNC control, CAD/CAM software and hardware including the advanced Tilter 5-Axis waterjet cutting head, Snapper camera for optimal positioning, Rounder kinematic compensation tool, and Straighter perpendicular angle tool. Flex is the only company in the United States offering these capabilities, catering to the intricate needs of diverse materials and cutting requirements, ensuring unparalleled accuracy and efficiency in waterjet cutting processes.
The unique, high productivity, long bed FlexCNC G-Series GM-20-06 Vertical Machining Center will also be under power at FABTECH, demonstrating heavy duty, accurate, high-speed cutting, milling, drilling and tapping of large parts, as well as machining round and square tubes on its 4th axis. The FlexCNC features a customizable bed length from 10’-to-80’, easily accommodating a wide range of long parts. The spindle moves, instead of the machine bed, permitting materials/parts of large weights and sizes. For optimal efficiency, a robust gantry-style machine architecture enables large part machining in a single setup. A monobloc welded steel frame with precision linear guideways provides a strong, rigid infrastructure which works in tandem with a comprehensive motion control system.
A range of balancing, drilling, and tapping arm products will also be demonstrated. For eliminating fatigue and repetitive motion injuries when grinding, Flex will demonstrate its B-33-RG Balance Arm for handheld grinders, designed to fit the specific grinder make/model. The Balance Arm offers full range of motion similar to natural movements, and also extends the life of the grinding tool and abrasive product. The B-33-RG has a counterbalance capacity of one-to-25 lbs., a reach range of 1″-to-72″ and 90 psi air pressure.
The FlexArm Mag Drill will also be demonstrated, showcasing how magnetic drilling can be simplified, while reducing operator fatigue and increasing safety and efficiency. The ergonomic Mag Drill Arm offsets the drill’s weight by effectively reducing up to 75 lbs. (34 kg) of strain on an operator’s body. The arm provides a working range of up to 100″ (2,540 mm) of horizontal reach and 52″ (1,320 mm) of vertical stroke, resulting in precision and versatility across a broad range of drilling operations.
Attendees can also see the versatile FlexArm REM-16 Electronic Tapping Arm with a Multi-Position Head that allows quick and easy switches between vertical and horizontal tapping. Renowned for its ability to produce accurate tapped holes while minimizing the risk of tap breakage, the REM-16 Electronic Tapping Arm has a maximum reach of up to 50″ (1,270 mm) and is designed for taps up to 5/8″ (16 mm) dia. The versatile FlexArm GH-45 Hydraulic Tapping Arm will also be highlighted, featuring a reach ranging from 20″ (508 mm) to 78″ (1,981 mm) and tap capacities from 3/8″ (9.5 mm) to 1.5″ (38 mm) dia.
Innovative Hydraulic Press Solutions Including Automation, Custom Applications
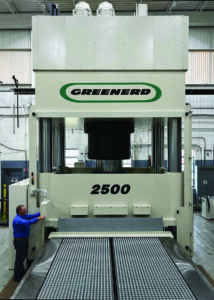
Greenerd Press & Machine Co. (Nashua, NH) has announced it will be highlighting the company’s extensive hydraulic press and automation capabilities at Booth S-30059. Application experts and design engineers from Greenerd will be available to discuss specific user applications and press requirements.
Greenerd designs and builds custom hydraulic presses with automation solutions for a range of industries and applications. One example that demonstrates these capabilities is a very large 2500 Ton Hot Forming Press.
Greenerd has designed, engineered and turnkey-installed this 2500 ton press featuring 10-foot square heated platens maintaining 500° (Fahrenheit) surfaces to +/- 5 degrees. The press comprises a seven-press order. The 2500 ton press features an innovative mold transfer system which significantly improves the ergonomic and safety dynamics for operators and reduces the press idle time between cycles.
“To meet the demands of today’s challenging applications, we are providing manufacturers with press solutions that are flexible, productive and reliable as well as often being quite large and complex,” said Greenerd Press & Machine Co.’s CEO Jerry Letendre. “For even greater manufacturing efficiency, we are able to provide our hydraulic press customers with turnkey, state-of-the-art robotic and other product handling solutions.”
Greenerd is a Tier 1 Industrial Authorized Robot System Integrator of FANUC America Corp., the industry’s leader in automated manufacturing equipment. The partnership gives Greenerd full access to the comprehensive offerings of FANUC Robots including all models, training and support, providing state-of-the-art automation solutions in short time frames. Complete, fully integrated production systems can be provided including simple raw material feeding systems, and robotic solutions for loading/unloading the press, the ability to perform an optional secondary part manipulation or process, automated inspection of parts and stacking finished products for downstream processes. The scope of automation can also encompass part inspection systems ranging from small sensors to complex camera inspections, and temperature monitoring/control of press and non-press related systems. Streaming critical production data to and from the press is also offered.
Greenerd’s extensive line of hydraulic presses are available in a variety of styles ranging from gap frame and straight-side to die-spotting and forging presses, with unlimited size and tonnage capabilities.
Discover Clinch Solutions In-die Tooling Systems
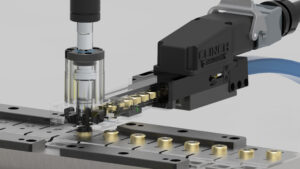
You may know Hutchison Tool Sales (Bensenville, IL) as the in-die tapping experts, but did you know that the same skilled toolmakers are also behind our innovative clinch solutions in-die tooling? We help eliminate your secondary welding or clinching processes with a solution that is part of your stamping die. We can help you install clinch nuts, studs, rivets and more. Take a look at this cost-effective solution for your fastening needs. Hutchison Tool Sales will be in Booth S-32045.
Our patented clinch tooling systems are seamlessly integrated into your dies, installing clinch fasteners as your stamped parts are produced. It might sound complex, but we’re here to simplify things for you. Our systems feature a straightforward design with standardized components, making them an easy and natural addition to your process.
Explore the unique features that set our systems apart from the competition. No matter which clinch process you choose, you’ll benefit from high-quality products crafted with exceptional precision and accuracy.
Automated 6-axis Structural Steel Robotic Beam Cutting Machine
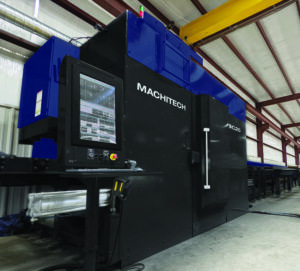
Machitech (Saint-Marc-des-Carrieres, Quebec, Canada) will feature its recently updated Beamcut BC25 at Booth S-11059. The BC25 is a user-friendly, versatile, robotic 3D CNC cell and platform for cutting metal parts and profiles from mild steel, stainless steel, and aluminum for virtually any structural steel shape. With high-definition Hypertherm plasma technology and FANUC robotics, the Beamcut BC25 is a totally automated 6-axis beam cutting system that provides maximum optimization of the manufacturing process, improving overall repeatability and accuracy while eliminating bothersome layout work before cutting, and time consuming and costly grinding after profiles are cut.
Along with the Beamcut BC25, Machitech will showcase a wide range of its equipment at FABTECH, including the Diamond Cut plasma table with the new Hypertherm XPR460 plasma, the Silver Cut plasma table with pipe-cutting attachment, and an electric press brake.
Along with an automated in-feed and out-feed system on a smaller footprint, the BC25 has unique features, including a Photo-Laser Measuring Device that allows split-second profiling and positioning to guarantee a precise cut. There is an advanced Windows-based operator control system that is easy-to-use and does not require special operator training. Proprietary Beamcut Soft software utilizes DSTV files from 3D profiling software and 2D DXF AutoCAD files. Once files are imported, Beamcut Soft automatically simulates the cutting sequence. An automatic cutting trajectory is created and verified on the drafting computer instead of the machine. The BC25 incorporates a safety enclosure and smoke trap that delimits the space required for robotic cutting and the circulation area around the system. A safety cabinet complies with OSHA safety standards. An optional dust collector is available to remove smoke and dust particles.
Machitech has more than 20 years of experience and more than 2,000 machines installed worldwide. Solutions offered include CNC plasma cutting systems, fiber laser cutting systems, light industrial CNC plasma cutting tables, heavy-duty industrial CNC routers, pipe cutting systems, robotic beam cutting systems and press brakes.
Innovative Press Room Solutions
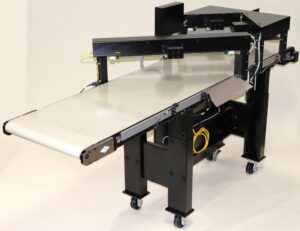
Pax Products, Inc. (Celina, OH) manufactures innovative press room equipment that is designed to eliminate issues and increase the productivity of metal stampers. Key items that will be on display in Booth S-33059 include:
- Automated Part-out Conveyor Demonstration: This belt type conveyor will be equipped with a vision sensor, unique parts diverters, and powered vertical and horizontal positioning.
- Scrap Removal Systems: Both a low-profile, belt-type conveyor and an electrically operated shaker-type conveyor will be in operation. This belt conveyor was developed for under-die, parts and scrap removal and its belt is only 3/8” above the bolster that the conveyor tray rests upon. The EGD conveyors, (shakers), utilize elliptical gears in a sealed oil bath to provide an extremely reliable design with a conveying rate of approximately 20 fpm. The EGD unit on display will be equipped with a quick release arm (QRA), which enables the operator to quickly and easily remove and re-install the arm (crossbar), without the use of tools. This feature enables the operator to access the press die area without reaching over the arm.
- Stock and In-die Lubrication Systems: Multiple types of lubrication systems, sprayers, and roller coaters will be on display. Pax’s spraying systems can be arranged for thick or thin lubricant, for in-die applications, and for lubricant recycling. Pax’s roller coaters have a slim design that fits into tight areas. The rollers on these units utilize polyethylene spacers to limit the compression on the rollers’ felt material, which enables the lubricant to better flow through the felt and increases roll life.
All of Pax’s products are “Designed for Stampers by Stampers.”
New Plate Processing Machine Combines High Performance Thermal and Mechanical Cutting
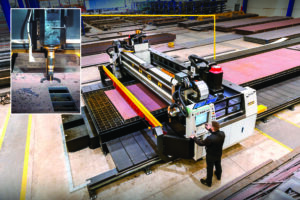
Tecoi USA (Longview, TX) will feature its powerful and versatile THOR® F (Tecoi Hyper Operative Range) plate processing machine at Booth S-24189. Designed for heavy-duty thermal cutting applications and having machining operations, THOR F integrates plasma and oxyfuel cutting with an optional beveling system, and an optional tube and profile lathe. Tecoi’s THOR F machine also combines plate cutting with edge preparation and numerous mechanical machining operations, including milling, drilling, tapping, countersinking, marking, etc.
High-performance THOR F plasma cutting operations include either one or two cutting heads and an optional beveling system, as well as oxyfuel cutting with up to 12 torches with an optimal bevel system, multiple marking options, and an auxiliary tube and profile lathe. Tecoi’s THOR F machine has a central XX axis with a path of 24” (610 mm) working on a robust double-beam design. It completes machining tasks with a fixed gantry and the option to fit up two machining heads. THOR F also integrates a unique table design for plate thicknesses up to 8” for thermal processing and drilling applications. One-half of the cutting table is magnetic, holding plates in place during machining operations for single pass edge milling for welding preparation of plates up to 2-3/8″.
The THOR F plate processing machine features Tecoi’s exclusive Bevel Arc® beveling system, accommodating angles of ± 50° with plasma or oxyfuel with maximum precision. The machine also features Tecoi’s Driltec® system for drilling and tapping with the option of an automatic tool charger while offering CAT 50 tool storage for five-to-32 tools. Tecoi’s THOR F cutting table can be equipped with dross collection under the grid and an independent chip collection system for recycling. The cutting grid is comprised of metal supports and a continuous lateral stop for maximum plate holding with a clamping system that keeps the plate in place during heavy milling applications. Slag can be collected with raisable drawers or by Tecoi’s Vibratec® system. Fumes are extracted using Tecoi’s Ecotec® filters and filtered dust is safely collected in the Dustec® system.
One-stop Source for Metal Fabrication Machinery
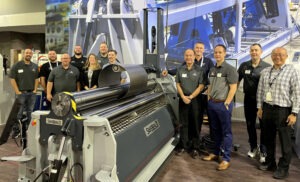
Roll. Punch. Form. Shear. Automate. Better. Trilogy Machinery Inc. (Belcamp, MD) is a nationwide leader in metal fabricating machinery and the exclusive distributor of top global brands like Sunrise, SweBend, Lemas, Synergy, and BSP.
Stop by Booth S-18151 to learn about the latest innovations in metalworking machinery and enjoy live demonstrations of a full range of equipment — including Ironworkers, bending rolls, processing lines, and more.
Whether you’re a small-scale workshop or a large manufacturing facility, we’ve got a machine to fit your needs. Count on our knowledgeable team to understand your business, recommend a solution, and support you throughout the lifespan of your purchase.
Streamline Your Coatings Process with Cutting-edge Tech
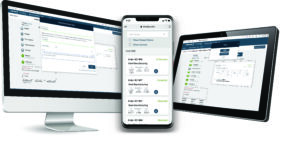
Valmont® Coatings (Omaha, NE) connects you to the entire coatings process through innovative technology, improving your experience and saving you valuable time. The newly enhanced Valmont Coatings Connector (VCC) Max is designed to optimize efficiency and keep you connected at every stage of the order process, delivering greater visibility — and confidence. No other coatings provider offers you the service, technology and visibility that we do. Valmont Coatings will be in Booth S-34070.
VCC Max automatically communicates your order status in real time on any device. Gone are the days of uncertainty. Through automatic email and text notifications, you will know exactly when your project is received, the status of each step, and when your order is ready for pickup or delivery.
www.valmontcoatings.com/vcc-max