A Range of new, Innovative Tools Cater to a Variety of Applications
The latest advancements in cutting tools; end mills, thread mills, thread formers and inserts, are transforming the machining industry.
Posted: August 27, 2024
Whether in aerospace, medical, automotive, or general engineering, versatile cutting tools engineered from the ground up offer the solutions necessary for optimized part processing and increased productivity. Improved tool designs and materials engineered for versatility across various materials and applications ensure highly accurate machining.
New Six-flute End Mill is Engineered for Titanium and Super Alloys
CERATIZIT USA, Inc. (Schaumburg, IL) has added to its OptiLine Series of solid-carbide end mills with the launch of a six-flute end mill. OptiLine end mills are versatile and optimized for various materials, machining strategies and part applications. The company designed and developed the new six-flute OptiLine end mill specifically for titanium and super alloys (ISO-S).
Engineered from the ground up, the OptiLine six-flute end mill features a premium substrate and advanced tool geometry. The end mill’s asymmetrical variable helix and variable index flute configuration ensures enhanced stability during cutting operations and includes chip splitters designed for applications involving 2.5 x D cutting lengths. Refined cutting edges and CERATIZIT’s Dragonskin coating technology improve chip control and reduce adhesion for longer tool life.
“We started with the six-flute’s foundation ensuring the substrate provides high toughness without sacrificing hardness,” said Scott Walrath, CERATIZIT business development manager, solid round tools. “The six-flute’s other key differentiator is the asymmetrical flute design because each tooth on a different helix angle delivers stability when machining a workpiece at varying angles.”
To accommodate customers across U.S. industry sectors, the new six-flute end mill will be available in inch assortments. OptiLine inch-type end mills, including the new six flute, are manufactured at CERATIZIT’s facility in Sacramento, Calif.
www.CuttingTools.CERATIZIT.com
Thread Mill Company Expands Its Line with a Range of New Tools
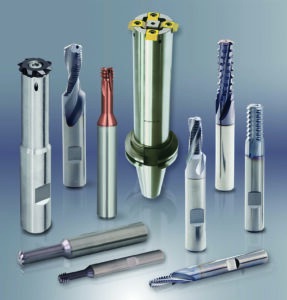
EMUGE-FRANKEN USA (West Boylston, MA), a leading manufacturer of high-performance taps, thread mills, end mills, drills, and other rotary tools, has introduced a significantly expanded line of thread mills, including innovative solutions for challenging threading applications and materials such as nickel alloys, titanium, high tensile strength steels, hardened high alloy steels, cast iron, cast aluminum and more. EMUGE-FRANKEN offers manufacturers a wide breadth of tooling options and industry-leading designs with five distinct thread mill tool families to address a range of machining requirements.
“To improve productivity and profitability in the most challenging threading applications, we are pleased to offer a significantly broadened line of new and unique thread mills,” said Marlon Blandon. “The science of thread milling is constantly progressing to efficiently machine tougher, higher cost materials and complex parts, and EMUGE-FRANKEN is continually innovating to meet the latest needs.”
The five EMUGE Solid Carbide Thread Mills distinct tool families include:
- THREADS-ALL™ family of thread mils that are designed for difficult threading operations and can make a range of thread sizes including smaller ones, available in single and multi-plane options. A complete line of 2xD and 3xD sizes provide maximum reach. THREADS-ALL/AERO thread mills are ideal for demanding materials and industries such as aerospace where nickel alloys, titanium and stainless steel are the norm.
- THRILLER style thread mills combine the drilling and thread milling process into one tool, eliminating the need for tool changes and saving machine tool carousel space. THRILLER thread mills are best suited for short-chipping cast aluminum alloys and cast iron. THRILLER-AERO thread mills are ideal for aerospace and nickel alloys, titanium and stainless steel materials.
- SHUR-THREAD™ thread mills are full profile cutters offering high process stability in a range of challenging materials. SHUR-THREAD is designed to cut one thread size and pitch, requiring a single 360° cutting rotation to complete the full threading operation.
- VARIO Full Profile Thread Mills are full profile thread mills manufactured to cut one specific pitch size but can also produce more than one thread size for universal material applications.
- GIGANT-IC™ carbide insert style thread mills facilitate quick set-ups and rapid changeovers when creating internal and external threads, right-hand and left-hand threads, as well as threads in very large holes. GIGANT-IC is suitable for cutting low- and high-alloyed steels up to 1,400 N/mm2, stainless steel and cast materials, alloys including aluminum, copper, magnesium and titanium and synthetics.
New EMUGE thread mills in the expanded line include:
- THREADS-ALL/MAX line of premium sub-micro grain solid carbide thread mills that are designed for maximum performance in high tensile strength and hardened materials from 44-to-66 HRC.
- THREADS-ALL/HEADED line featuring circular thread milling bar/bodies with exchangeable face inserts, provide an excellent modular solution for milling larger thread dimensions in stainless steel, titanium, nickel alloys, cast iron and hardened high alloy steels >25 HRC, and mold and tools steels.
- THRILLER-MAX thread mills are designed to dramatically improve tool life and performance in hard-to-machine, high tensile strength materials 44-to-66 HRC.
- VARIO-Z External Thread Mills are specifically designed to produce external threads in a wide range of materials and applications.
- VARIO SKIP Tooth Thread Milling Cutters with alternating tooth rows are designed to reduce radial cutting forces and provide an option to remove the incomplete thread.
New Turning Inserts for Small Parts and Medical Machining
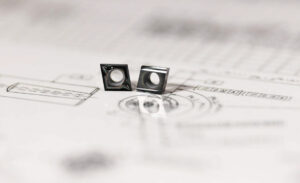
Kennametal Inc. (Pittsburgh, PA) is expanding its turning portfolio with the introduction of TopSwiss Turning Inserts. Uniquely designed for Swiss-type small parts machining, TopSwiss Turning Inserts deliver Kennametal customers with an insert product line engineered for low feed, high depth-of-cut applications across industries including medical, aerospace and defense, general engineering and transportation.
This new turning portfolio features:
- Four new carbide grades, one new cermet grade and seven new geometries.
- Straight and curved cutting edges for stable cuts and smooth chip flow in low feed, high DOC applications.
- Polished finishing geometries for increased welding resistance and improved surface finishing.
- Medium and finishing wiper geometries for increased feed rates and superior surface quality.
- Several geometries with high chip breaker walls and large pockets for better chip evacuation.
“We’re continually building on our turning portfolio with next level solutions that meet the application needs of our customers globally,” said Scott Etling, vice president of global product management. “TopSwiss Turning Inserts are a testament to this continued commitment to innovation and to delivering customers high performance products. These inserts are our latest solution for shops running low feed, high depth-of-cut applications and looking to achieve better chip evacuation and surface finishing.”
Expansion of an Indexable Insert Grade
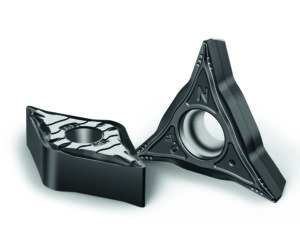
Walter USA LLC (Greer, SC) has expanded its WSM01 grade for indexable inserts to include the FM4, FM5, FM6 and MM4 geometries. The FM5 geometry in the WSM01 grade is available with the CNMG, DNMG and WNMG basic shapes. WL25 indexable inserts with the FM4 or MM4 geometry are also available in the WSM01 grade, as well are the FM4, FM6 and MM4 geometries with further radii.
The grade features a physical vapor deposition (PVD) high-power impulse magnetron sputtering (HiPIMS) titanium aluminum nitride (TiAlN) coating for effective machining stainless steels and heat-resistant super alloys (ISO M and S material groups). The thin yet very dense TiAlN coating provides excellent bonding on sharp cutting edges.
When comparing the coated surface of the HiPIMS PVD process to the standard PVD process, the HiPIMS process creates an extremely smooth surface while the standard process causes increased droplet formation and irregularities. An extremely smooth rake face enables low friction, reducing built-up edge. In addition, the WSM01 grade has a micrograin substrate, which is extremely hard to protect against abrasive wear and flank face wear.
When applying the FM5 geometry for finishing stainless materials and super alloys, Walter recommends a feed rate (f) of 0.004”-to-0.233” (0.10 mm-to-0.60 mm/rev.) and an axial depth of cut (ap) of 0.012”-to- 0.118” (0.3 mm-to-3.0 mm). The recommended feed for the FM6 geometry is from 0.003”-to-0.013” (0.08 mm-to-0.32 mm), and the recommended depth of cut ap is 0.012”-to-0.098” (0.3 mm-to-2.5 mm). It is a universal geometry for finishing and medium machining operations.
The machining parameters for the MM4 geometry are a feed of 0.003”-to-0.013” (0.08 mm-to-0.32 mm) and an ap of 0.016”-to-0.138” (0.4 mm-to-3.5 mm). The geometry is for machining long-chipping workpiece materials. The WL25 indexable inserts with the FM4 or MM4 geometry are for copy turning/profiling operations of undercuts and recesses up to 30°, 50° (W1011/W1211) and 72.5° (W1010/W1210). They are a replacement for the ISO VBMT, VCMT and DCMT indexable inserts.
Potential benefits of the expanded range include maximum tool life when cutting high-strength materials, optimum surface qualities thanks to the HiPIMS coating and the production of high-quality parts over a long tool life.
New Solutions for Optimized Part Processing
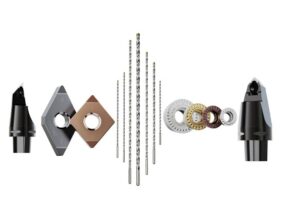
Two new Seco Tools LLC (Troy, MI) grades of PCBN inserts offer ideal performance in high-volume production of automotive and other industry components. The CH1050 grade is designed for finishing and the CH2581 for semi-interrupted cuts. With a substrate grade and unique Seco nanolaminate PVD coating designed to achieve high surface quality requirements, CH1050 also offers high-accuracy edge prep through a new grinding process. Designed for extended tool life and lower cost per part, CH1050 promotes high output and reduced scrap or rework. CH2581 achieves greater process stability and reduced tool breakage with a versatile, forgiving grade specifically designed for semi-interrupted cuts. Its high-accuracy edge prep and next-generation Seco PVD coating enable faster speeds and higher throughput for reduced part costs.
Seco Tools also offers the MF2 chip breaker on RCMT/RCGT round, positive-style ISO-turning carbide inserts with chip control. Many round turning inserts suffer from poor chip control, but the Seco MF2 chip breaker on RCGT/RCMT inserts maintain favorable chip control at higher speeds and feeds, especially with dynamic turning. One series of stable, durable carbide round insert grades handles a wide range of turning operations from roughing to finish turning. Seco’s unique chip breaker geometry and strong insert shape provide versatile, reliable performance in tough operations, including heavy intermittence and rough skin. In a general engineering environment with materials ranging from smeary low-carbon steels to stainless steels, titanium and heat-resistant super alloys (HRSA), these versatile inserts outperform pointed tools.
On parts with wide, deep grooves, pockets or cavities — even in difficult-to-cut materials — MF2 chip breaker on RCMT/RCGT inserts tackles complex parts with fast production.
New Solid Carbide Milling Cutters
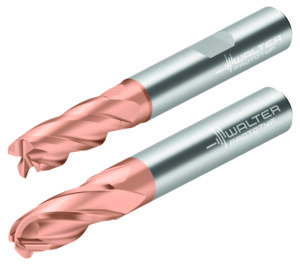
Walter USA LLC (Greer, SC) has unveiled the ME232 and ME432 Perform solid carbide milling cutters to add to its range of solid milling cutters. The tools can be used universally for diverse milling operations with various workpieces, meaning one tool is appropriate for a large range of material types. The Perform cutters are designed to be highly economical and are made with the WJ30ED universal milling grade.
The ME232 Perform has a cutting diameter (Dc) from 1/8″-to-¾”, and from 2 mm-to-20 mm, and is available with two, three, four, five or six effective flutes (z2, z3, z4, z5 or z6). The z2 and z3 tools are primarily for slot milling and profile milling; the z4 is for ramping, slot milling and helical milling; the z5 is for roughing and finishing; and z6 is for dynamic milling and finishing. These series offer cutting-edge length (Lc) is from 1 × Dc to 3 × Dc.
The ME232 is suitable for milling steel, stainless steel, cast iron, nonferrous metals and heat-resistant super alloys (ISO P, M, K, N and S material groups). The tools can be used in a range of industries, including mechanical engineering, automotive, energy and tool, mold and die making. The ME232 Perform features the newly developed high-performance cutting (HPC) geometry, with helix pitches tailored to the number of teeth. For example, the z4 cutter has a variable helix geometry with 35° and 38° helix angles.
In the application testing or milling 4140 steel and stainless steel, the ME232 cutter increased the tool life distance 244% and 340%, respectively, versus the competitor.
The ME432 Perform is a ball-nose endmill for roughing and finishing freeform surfaces. The cutting diameter range is from 1/16″-to-5/8″, and from 1 mm-to-20 mm. It is available with two or four effective cutter teeth (z2 or z4) and has a 30° helix angle.
New Turning Insert Grades for HRSA Machining
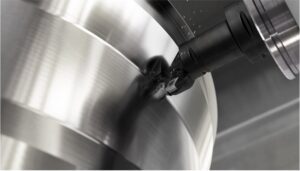
When turning aero-engine components, the surface requirements are high but no longer difficult to achieve, thanks to Sandvik Coromant’s (Mebane, NC) new insert grades GC1205 and GC1210. Together, they cover a large application area within last-stage machining (LSM) and intermediate-stage machining (ISM).
There are several key features that help in working with the high-level performance of heat-resistant superalloy (HRSA) materials. A hard, fine-grained new substrate, the latest physical vapor deposition (PVD) coating technology and optimized edge-line integrity provide increased flank wear and secondary notch wear resistance, superior edge-line security and reduced flaking.
“For our customers, this translates into possibilities to run the inserts at higher cutting speeds with GC1205 and increased tool life with GC1210,” said Martin Saunders, global product application specialist for turning at Sandvik Coromant. “Additionally, it ensures consistent and predictable tool life while reaching the required surface integrity demands for critical aerospace components.”
Typical aero-engine components that the grades can machine are gas turbine discs, casings, blisks, spools, shafts and blades. But these grades also prove to be a great choice in demanding applications such as power generation turbines and medical implants made of cobalt-chrome. Saunders continued, “The release of these two new grades offers the opportunity to increase cutting data while also prolonging tool life predominantly in last-stage machining and intermediate-stage machining of aerospace and medical components.”
The grades complement each other thanks to an overlap in the assortment. GC1205 is a finishing grade for machined surfaces in LSM and ISM applications. GC1210 complements GC1205 when more toughness is required and is mainly used in ISM applications for nonmachined surfaces.