Waterjet Cutting for Multiple Materials
For fabricators in search of new opportunities, and for customers who want shops that provide greater value, waterjet cutting is too important to overlook.
Posted: February 16, 2024

Waterjet cutting uses a highly pressurized stream of water to fabricate parts from more than just metal materials. It’s fast and accurate but sometimes misunderstood. Among glass fabricators and metalworkers, waterjet cutting usually refers to abrasive waterjet cutting, a version of the process that mixes a garnet abrasive with a highly pressurized stream of water. Among rubber and plastic fabricators, waterjet cutting typically refers to pure waterjet cutting, which uses a highly pressurized stream of water without an abrasive material.
Despite their differences, both types of waterjet cutting offer three key advantages. First, there isn’t any tooling to wait for or pay for. That makes it a cost-effective choice for projects ranging from iterative prototypes to low-to-medium volume production. Second, waterjet cutting produces fast cuts, smooth joints, clean edges, chamfers, angles, and perfect 90° corners. Third, because waterjet cutters are computer-controlled, a fabricator can use an engineer’s computer-aided design (CAD) file to create a computer-aided manufacturing (CAM) file that controls the machine with precision.
Abrasive Waterjet Cutting vs. Pure Waterjetting
Abrasive waterjet cutting is often used with harder metals such as steel, stainless steel, and titanium. Applications include ballistic panels for military vehicles, titanium parts for airplanes, and dies made of tool steel. Abrasive waterjet cutting is also used with softer metals like aluminum and with composites, ballistic glass, and Kevlar. Still, these aren’t its only applications. Rubber products that contain metal inserts and thicker, softer elastomers also use abrasive waterjet cutting instead of pure waterjet cutting.
Pure waterjet cutting is used mainly to convert softer, thinner materials like rubber and plastic sheets. It’s also used to cut rubber and plastic extrusions, lengths of material that are forced through a shaped die under high pressure and that have a fixed cross-dimensional section. Thermal and acoustic foams support pure waterjet cutting, and so do thin metal foils and industrial fabrics. That’s important since foils and fabrics can be laminated to insulating rubber materials to create products like engine bay insulation.

Which waterjet cutting technique is right for your shop or application? Material type and thickness are critical, but they aren’t the only considerations. If a smooth surface finish is a requirement, then pure waterjet cutting has the edge. This abrasive-less process also has lower consumable costs. Yet abrasive waterjet cutting vs. pure waterjet cutting doesn’t have to be an either/or proposition. That’s true for fabricators and metalworkers, but also for their customers. (See Figure 1.)
Equipment Selection and Use
For shops who want to win new business and for customers who want more value from suppliers, equipment selection and use are especially important. Some equipment is capable of just one type of waterjet cutting, but there are also machines that can cut both with and without an abrasive. Today, there are parts fabricators who are using both processes to provide customers with a complete solution.
For example, consider the case of rubber and metal assemblies. Rubber can be molded over metal to form a permanent bond, but what if the rubber needs to be removable? With equipment that supports both waterjet cutting processes, a fabricator can cut a metal arm, cut a rubber gasket, and then assemble the gasket over the arm like a sleeve. A fabricator can also cut stainless steel for kitchen tables and then cut the rubber edge trim that gets installed along the table’s edges. The fabricator wins more of the customer’s business, and the customer enjoys one-stop shopping.
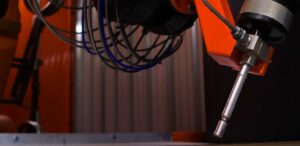
How could you put waterjet cutting to work in your shop, with or without an abrasive? Or, if you need to outsource parts fabrication, what does your manufacturing partner need to know in order to get the job done? With machines that support both abrasive waterjet cutting and pure waterjet cutting, there are adjustments to make when switching back and forth. Specifically, there are three key considerations: cutting heads, cutting surfaces, and water pressure. It’s also important to perform regular cleanups and periodic maintenance.
Cutting Heads and Cutting Surfaces
Figure 2 shows a waterjet table that’s configured for abrasive waterjet cutting. A special abrasive waterjet head is connected to a tube that supplies the abrasive material (i.e., sand). This material is stored in a pressurized reservoir that, depending on the size of the reservoir and the frequency of the equipment’s use, may need to be refilled daily. When it’s time to switch to pure waterjet cutting, an operator replaces this cutting head with one that doesn’t have a sand supply line. That requires some machine downtime. (See Figure 2.)
Machines that are equipped for abrasive waterjet cutting and pure waterjet cutting also use two different cutting surfaces. In Figure 3, the red arrow shows how the waterjet table has metal slats with gaps of several inches between them. These slats form channels that hold the fluid slurry that is dispensed. Because the cutting head doesn’t remain in one position for long, abrasive wear on the slats is gradual. Eventually, however, the slats will become worn, chipped, and require replacement. Again, this involves some machine downtime.
When it’s time for a fabricator to switch to pure waterjet cutting, plastic supports are laid on the table in between the metal slats. In Figure, a red arrow points to these supports, which have small openings so that the dispensed water can pass through. These support structures are necessary because pure waterjet cutting is generally used with softer materials like rubber and plastic. The harder and stiffer materials that are fabricated with abrasive waterjet cutting can sit atop the slats, but that won’t work with a thin, flexible sheet.
Water Pressure and Cleanups
During waterjet cutting, a pump generates water pressures that are measured in tens of thousands of pounds per square inch (PSI). Next, the waterjet cutter converts this pressure into velocity. Water then travels into the cutting head and through a jewel orifice that restricts the flow of this high-pressure fluid. Because there’s no tooling to configure, the advantages of waterjet cutting include the elimination of setup charges. Still, it’s important to use the right PSI for the specific cutting process.
For pure waterjet cutting, the water pressure ranges between 20,000 and 60,000 PSI. That’s a wide range, but the proper pressure depends on the fragility of the material that’s being cut. With abrasive waterjet cutting, the pressure isn’t so material dependent. Generally, it’s 60,000 PSI. When a shop uses abrasive waterjet cutting, it’s normal for some dust residue to be left on and around the table. A quick cleanup is required, but it’s typically not extensive.
Eventually, however, the waterjet table will fill with sand. That’s when the fabricator or metalworker needs a contractor with special siphoning equipment. The vacuum truck and heavy-duty hose that are used are not unlike what’s required for cleaning chemical toilets. If the waterjet table is very full, the cleanup process may take all day. Strong suction is especially important because the abrasive material between the metal slats is more like quicksand than playground sand.
Waterjet Cutting Advantages and Applications
Waterjet equipment that supports both pure waterjet cutting and abrasive waterjet cutting can have three axes or six axes. Three-axis, gantry-style machines are ideal for small to medium-sized parts, including components with thin, tapered ends such as small hooks with bolt holes. In Figure 4, 6-axis waterjet cutting uses an industrial robot that supports a larger work envelope and can cut larger parts. Applications include ballistic glass for windshields on military vehicles.
Compared to other types of cutting operations, waterjet cutting has distinct advantages. For example, the guillotine cutting that’s used for rubber profiles with metal inserts can deform the rubber and produce cuts with inconsistent quality. Die cutting can also put pressure on a rubber profile and cause edge distortions, especially with softer elastomers. With metal parts, laser cutting can create heat-effected zones and cause material hardening. CNC cutting requires tooling and may also distort the workpiece.
For fabricators in search of new opportunities, and for customers who want shops that provide greater value, waterjet cutting is too important to overlook. Other cutting processes have their advantages, of course, but both pure waterjet cutting and abrasive waterjet cutting can produce high-quality parts quickly and cost-effectively. Plus, with equipment that supports waterjet cutting both with and without an abrasive, cutting dissimilar materials like metal and rubber is no longer an either/or proposition.